基本的な考え方
日清紡グループは、「行動指針」に環境負荷への認識と配慮を掲げ、自社での省エネルギー対策はもとより省エネ型の技術・製品・サービスを提供し、すべての人びとにとって安心・安全な社会を誠実に実現します。
【主な対策】
- ①ISO14001の活動を通じ、エネルギーの消費抑制活動を推進
- ②設備更新時に環境配慮型設備を選択、改善活動による省エネルギー対策を持続的に実施
- ③計画的な照明のLED化
- ④新建造する建屋・倉庫へのさまざまな省エネルギー設備導入と、空調で消費するエネルギー削減の追求
推進体制については、「環境マネジメント」にあります「推進体制」の記載をご参照ください。
日清紡グループの具体的な取り組み
第5期3カ年環境目標(達成年度2024年度)
日清紡グループでは、2024年度を達成年度とする「第5期3カ年環境目標(第5期サステナビリティ推進計画)」では、環境経営の推進を重点活動項目とし、「売上当たりの使用エネルギー削減」を推進するために、以下の目標・KPI※ を定めました。
※ KPI:Key Performance Indicator 業績管理指標・業績評価指標
「売上当たりの使用エネルギー削減」 2014年度比 15%以上削減
PDCAを回しながら削減量を管理して計画的に対策を進めた結果、当社グループの2024年度の状況は、2014年度比39%削減となりました。各事業ともに省エネルギー対策が順調に推進されたことに加え、使用エネルギーの大きかったブレーキ事業の子会社であったTMDグループを譲渡したこと、マイクロデバイス事業の減産などが主な要因です。
第6期3カ年環境目標(達成年度2027年度)
2027年度を達成年度とする「第6期3カ年環境目標(第6期サステナビリティ推進計画)」では、第5期の取り組みを踏襲しKPI値の引き上げをおこないました。
「売上当たりの使用エネルギー削減」 2014年度比 30%以上削減
「3カ年環境目標」の概要については「環境マネジメント」をご覧ください。
「サステナビリティ推進計画」の概要については「サステナビリティ推進計画とKPI」をご覧ください。
燃料別エネルギー使用量
日清紡グループの2024年度エネルギー使用量実績は、6.41 百万GJと前年度比26%減少しました。売上当たりのエネルギー使用量は、12.96 GJ/百万円となり、前年度比20%減少となりました。各事業ともに省エネルギー対策が順調に推進されたことに加え、エネルギー使用量が多いブレーキ事業の子会社であったTMDグループ譲渡やマイクロデバイス事業での減産が主な要因です。
燃料別では、使用エネルギー全体の86%が電力、8%がガスでした。
エネルギー使用量と売上当たりのエネルギー使用量の推移
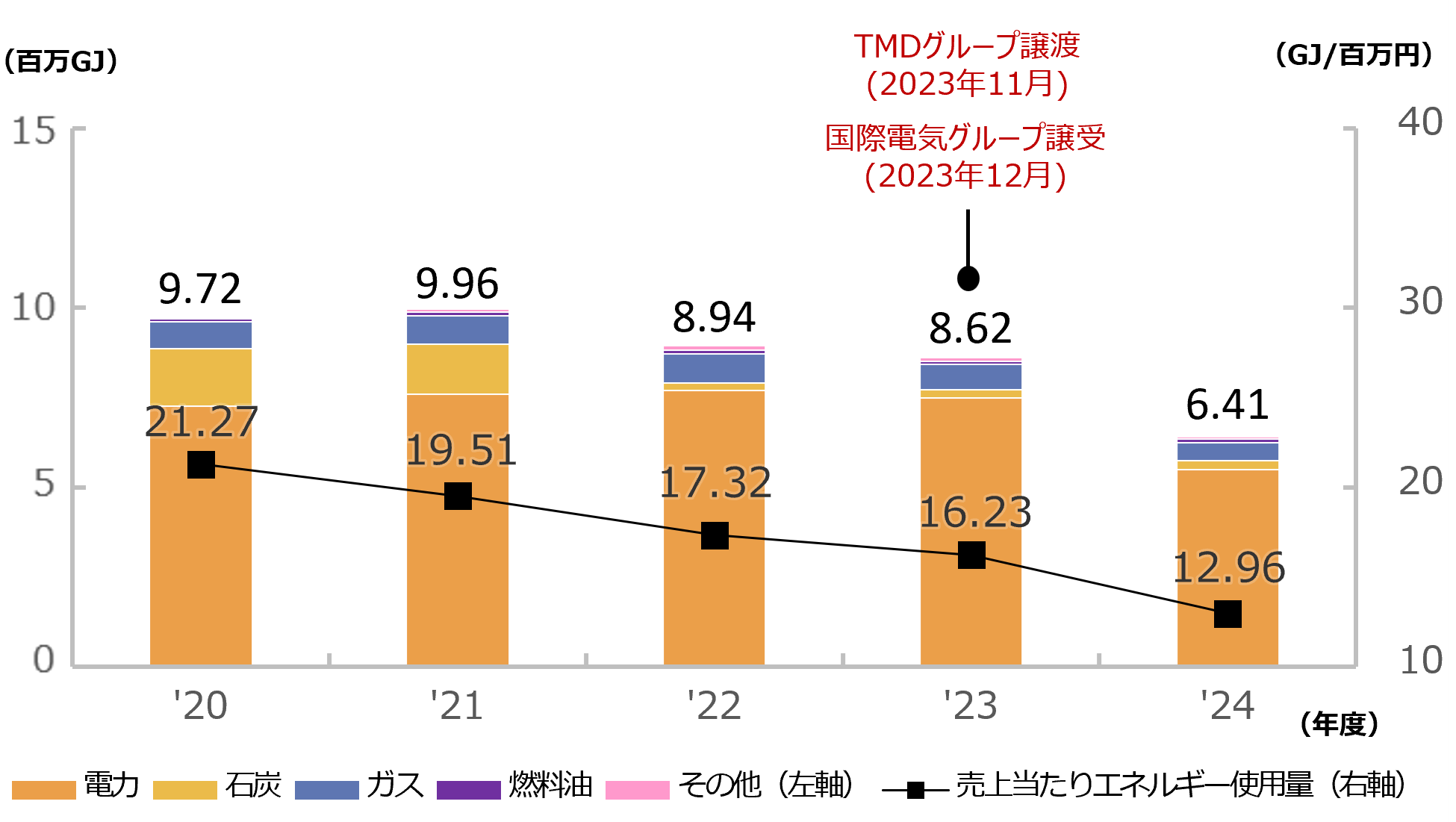
※1 当社は2023年11月30日に、連結子会社であったTMDグループを譲渡したことにより、連結の範囲から除外しています。このためTMDグループは2023年11月度までのデータを集計対象としています。
※2 当社は2023年12月27日に、国際電気グループを連結の範囲に含め、2024年度からデータ集計の対象としています。
※3 当社は2024年11月28日に、無線・通信事業における子会社としてARGONICS GmbHおよびARGONAV GmbHを連結の範囲に含めましたが、2024年度データ集計の対象外としています。
事業別エネルギー使用量
事業別でエネルギーを最も多く使用したのはマイクロデバイス事業(1.82百万GJ 前年度比13%減少)で、次いで繊維事業(1.53百万GJ 前年度比12%減少)でした。
事業別エネルギー使用量
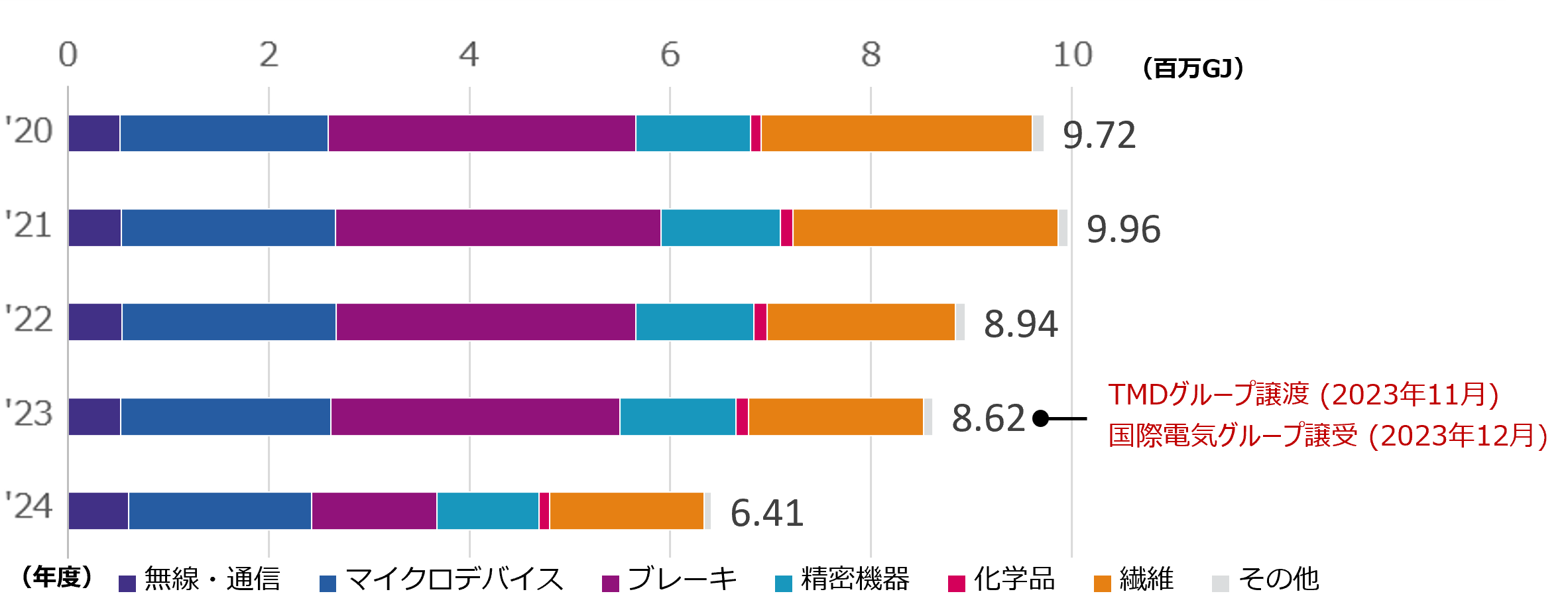
※1 当社は2023年11月30日に、連結子会社であったTMDグループを譲渡したことにより、連結の範囲から除外しています。このためTMDグループは2023年11月度までのデータを集計対象としています。
※2 当社は2023年12月27日に、国際電気グループを連結の範囲に含め、2024年度からデータ集計の対象としています。
※3 当社は2024年11月28日に、無線・通信事業における子会社としてARGONICS GmbHおよびARGONAV GmbHを連結の範囲に含めましたが、2024年度データ集計の対象外としています。
省エネ法事業者クラス分け評価制度
事業者クラス分け評価制度は、省エネ法に基づき定期報告を提出する全ての事業者をS・A・B・Cの4段階へクラス分けし、事業者自らが省エネ活動の状況を客観的に理解するために行われています。最優良のSクラスは、エネルギー使用原単位の5年度間平均1%以上の低減があった事業者です。この結果は毎年、資源エネルギー庁ホームページで公表されており、今回は、2020年度~2024年度の報告が評価の対象です。
2024 年度の省エネ法事業者クラス分け評価の結果が発表され、日清紡グループからは下記8社が最高評価であるS評価を受けました。
最優良のSクラス
- 日清紡ホールディングス(株)
- 日清紡マイクロデバイス(株)
- 日清紡マイクロデバイスAT(株)
- 日清紡マイクロデバイス福岡(株)
- 日清紡ブレーキ(株)
- 日清紡メカトロニクス(株)
- 南部化成(株)
- 日清紡ケミカル(株)
グループ会社における活動事例
照明器具のLED化
日本無線(株)では、上田物流センターの照明器具のLED化を推進しています。2021年から5カ年で物流センター内すべての照明をLED化する計画です。
計画開始から4年目にあたる2024年度は、北棟2階および5階に設置されている照明器具532台のLED化を実施しました。今回のLED化により、年間で130 MWhの電力使用量の削減を見込んでいます。
2024年末で物流センター内に設置している照明器具1,894台のLED化作業が完了し、物流センター内の照明器具の98.7%がLED化されました。これにより、LED化前と比較すると、439 MWhの電力使用量を削減できたことになります。
2025年は、残っている北棟4階の非常照明と外構エリアの25台についてLED化を行います。これにより上田物流センターのLED化は計画通り完了します。
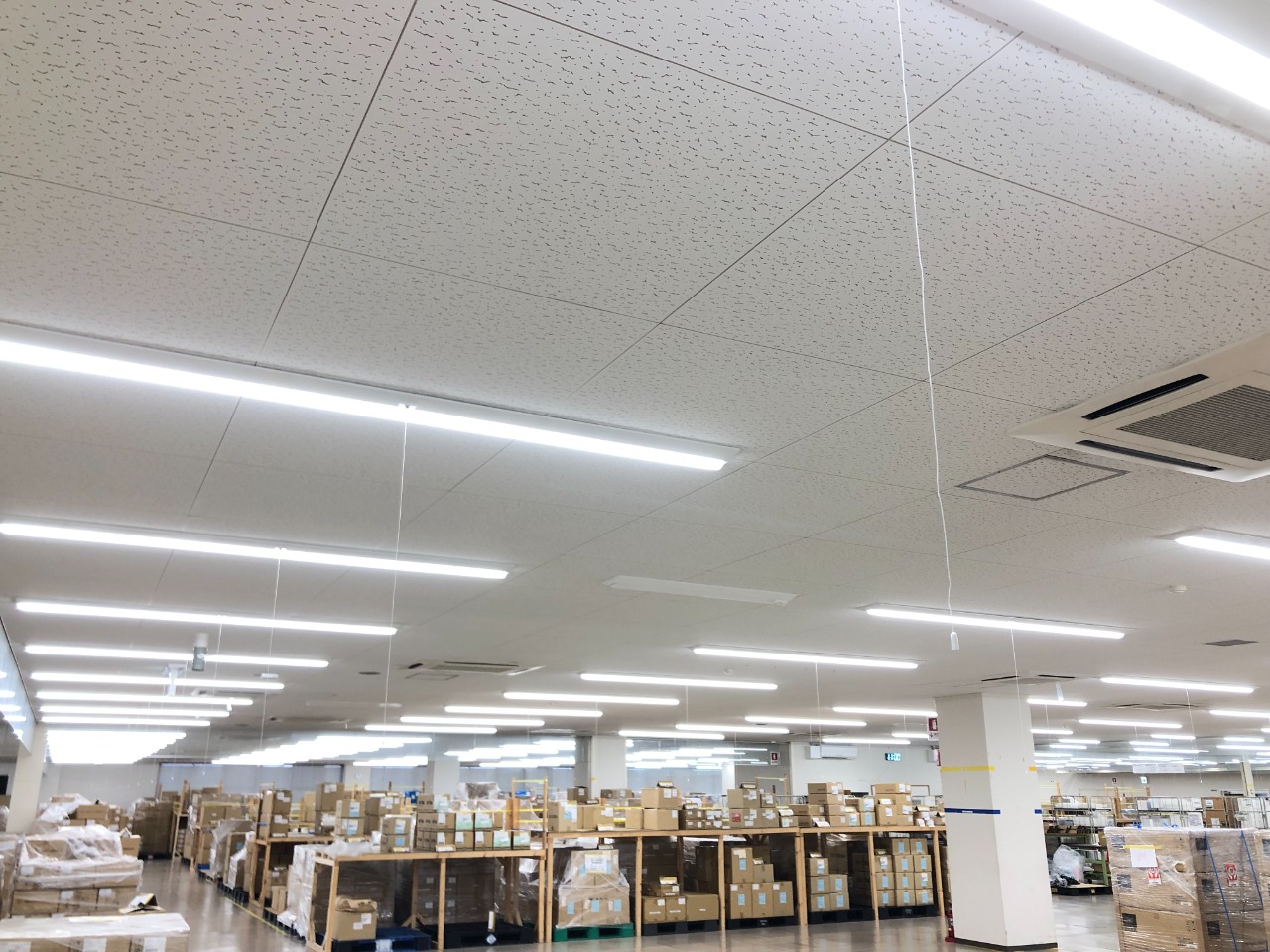
空調室外機の遮熱・断熱塗装施工による省エネ対策
(株)国際電気 東京事業所では、空調機の省エネ対策のため、WW棟の空調室外機89台、コンクリート床面445m2および冷媒配管に対して、遮熱・断熱効果のある塗装を施工しました。
2024年4月に第1期として4分の1のエリアの施工を実施しました。その効果を確認したうえで、12月に残りの4分の3のエリアの施工を実施し、WW棟屋上設置のすべての空調機への施工が完了しました。これにより、空調室外機の電力使用量の10%程度の削減効果を見込んでいます。
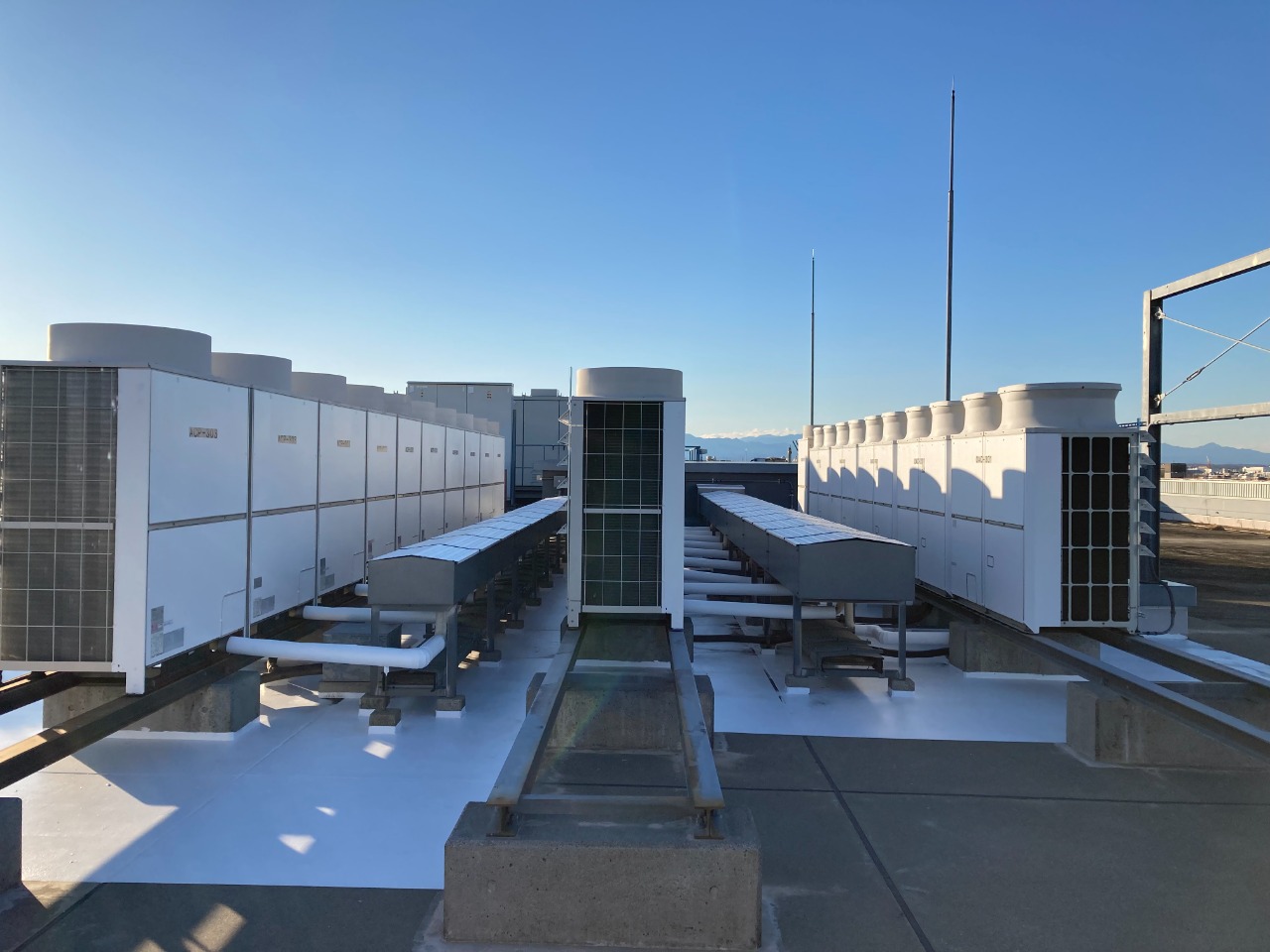
生産設備冷却水ポンプのインバータ制御による省エネ
日清紡マイクロデバイス(株) 川越事業所では229棟クリーンルーム生産装置向け間接冷却水の送水ポンプを4台設置しています。そのポンプに異常停止や急激な圧力低下などが生じた際、これまでは圧力調整をバルブで行い、圧力低下や変動による生産装置への影響が出ないように通常より高い圧力で送水していたため、過剰な電力消費が生じていました。
この課題解決策として、圧力調整をバルブから送水圧力の常時監視制御によるインバータ運転へ変更し、モーターの回転数を制御するように変更しました。これにより、一定の圧力を保つことができ、年間約270 MWh(温室効果ガス排出量87.0 t-CO2)の削減を見込むことができました。
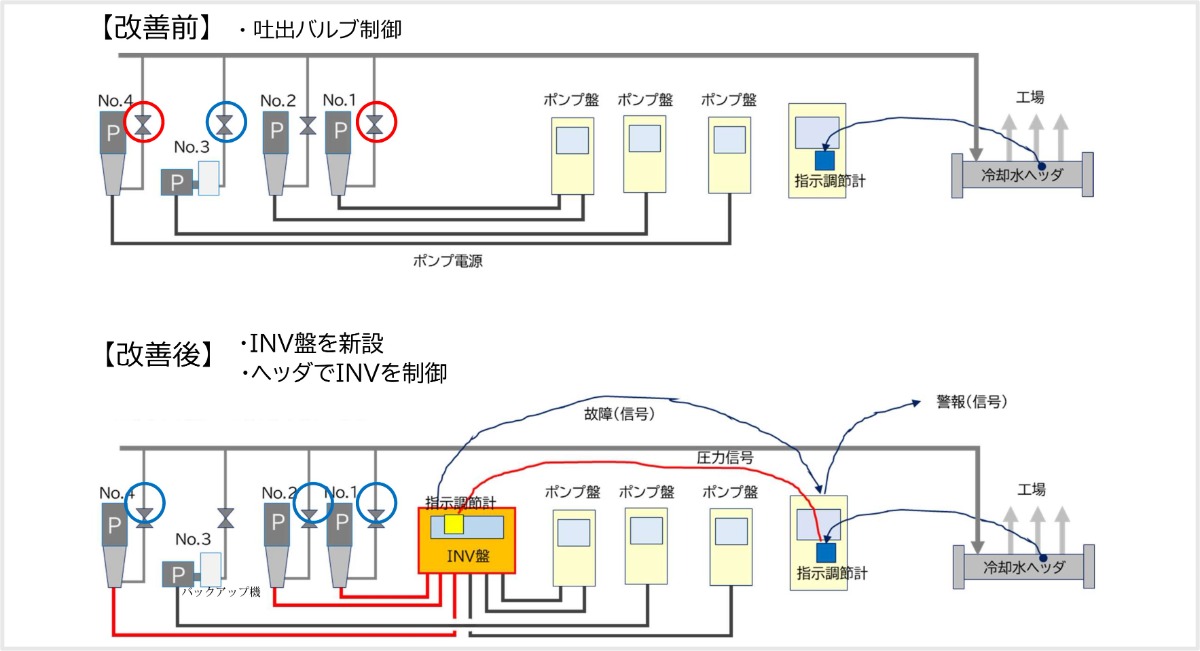
酸排水処理方法変更による都市ガス削減
日清紡マイクロデバイス(株) やしろ事業所では、生産ラインから排出される酸排水を蒸気処理し、下水放流していました。この蒸気処理を薬品処理に変更することで、使用していた蒸気が削減され、約180千m3/年の都市ガスの削減を実現しました。
生産ラインから排出される酸排水は、過酸化水素を含有しているため、アルカリ排水とともに、蒸気による熱分解処理を行っていました。酸排水はアルカリ排水に比べると、2.5倍の排水量があり、多くの蒸気を使用していましたが、過酸化水素を含有している酸排水の処理をアルカリ排水と分離し、薬品処理に変更することで、蒸気の使用を減らすことができ、その蒸気を作るための都市ガスの使用を削減することができました。蒸気使用量が減ったことにより、約2千m3/年の水使用量削減にもつながりました。
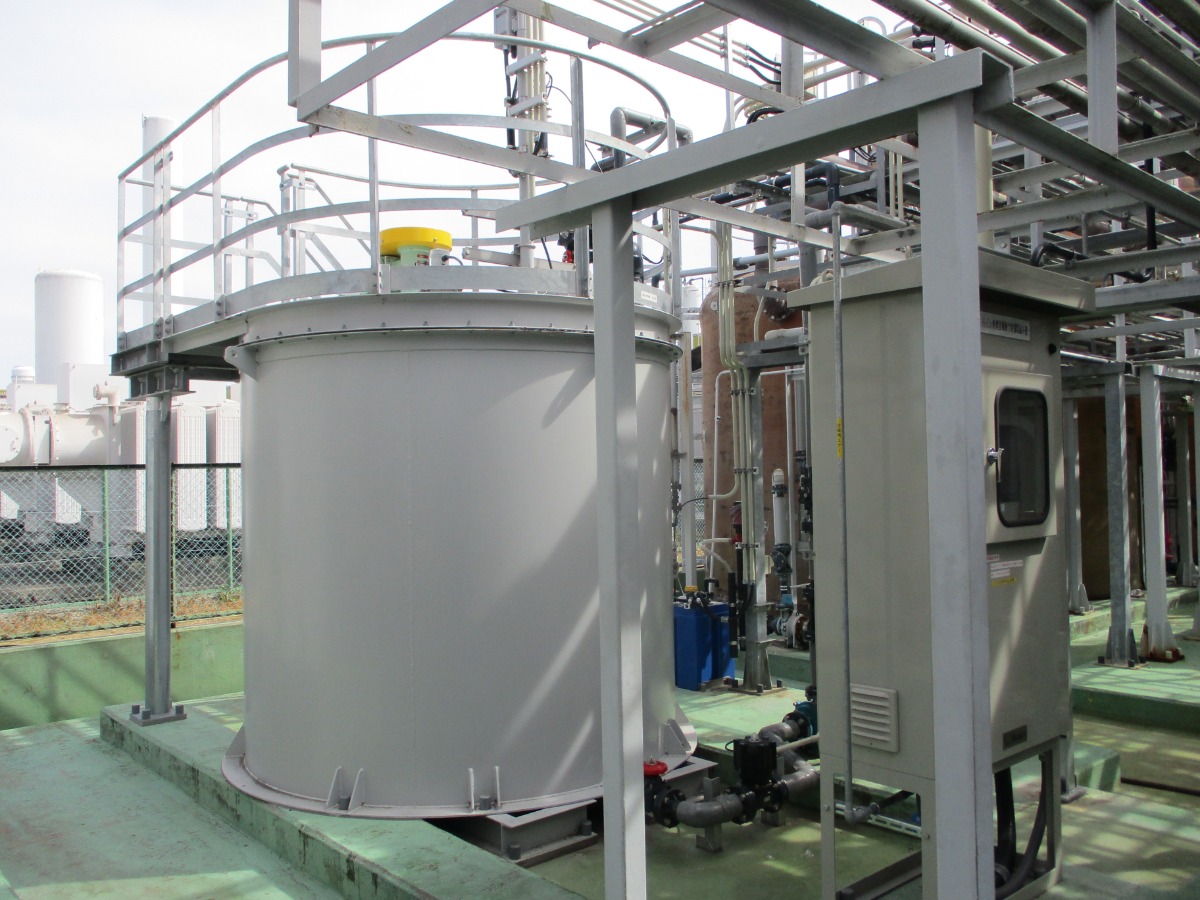
動力・生産設備の電気使用量削減
日清紡マイクロデバイス福岡(株)では、2024年度末までに前年度比1%以上(2,55 MWh/年)および2014年度比15%(5,322 MWh/年)以上の電力削減を目標に、動力・生産設備に対し、以下の省エネルギー対策を実施しました。
- ①常温冷却水送水ポンプ設備37 kW IE3モーターにインバータ制御盤を追加し、周波数調整による運転で79 MWh/年(温室効果ガス排出量30 t-CO2/年)削減
- ②純水設備RO高圧ポンプNo.2更新に併せ30 kWモーターをIE3(トップランナー)に変更し7.5 MWh/年(温室効果ガス排出量2.9 t-CO2/年)削減。
- ③拡散炉の処理待ち待機中に、入口からの放熱による電力消費を防ぐため、石英ボートを炉内収納後に、エンドキャップで蓋をする対応を年間183日実施したことで、約7.3 MWh/年(温室効果ガス排出量2.8 t-CO2/年)削減。
- ④生産非稼働期間、製品待ちの長い設備に対し、拡散炉スタンバイ温度を変更したことで、約118 MWh/年(温室効果ガス排出量45 t-CO2/年)削減。
また、生産負荷減(前年度比21%減)による生産非稼働日の実施などもあり、2024年度の全体の電力使用量実績は、25,477 MWh/年となり、前年度比10.0%減の2,876 MWh/年(温室効果ガス排出量1,093 t-CO2/年)および2014年度比で27.9%減の9,838 MWh/年 (温室効果ガス排出量3,738 t-CO2/年)の削減につながりました。今後も省エネ対策を継続実施していきます。
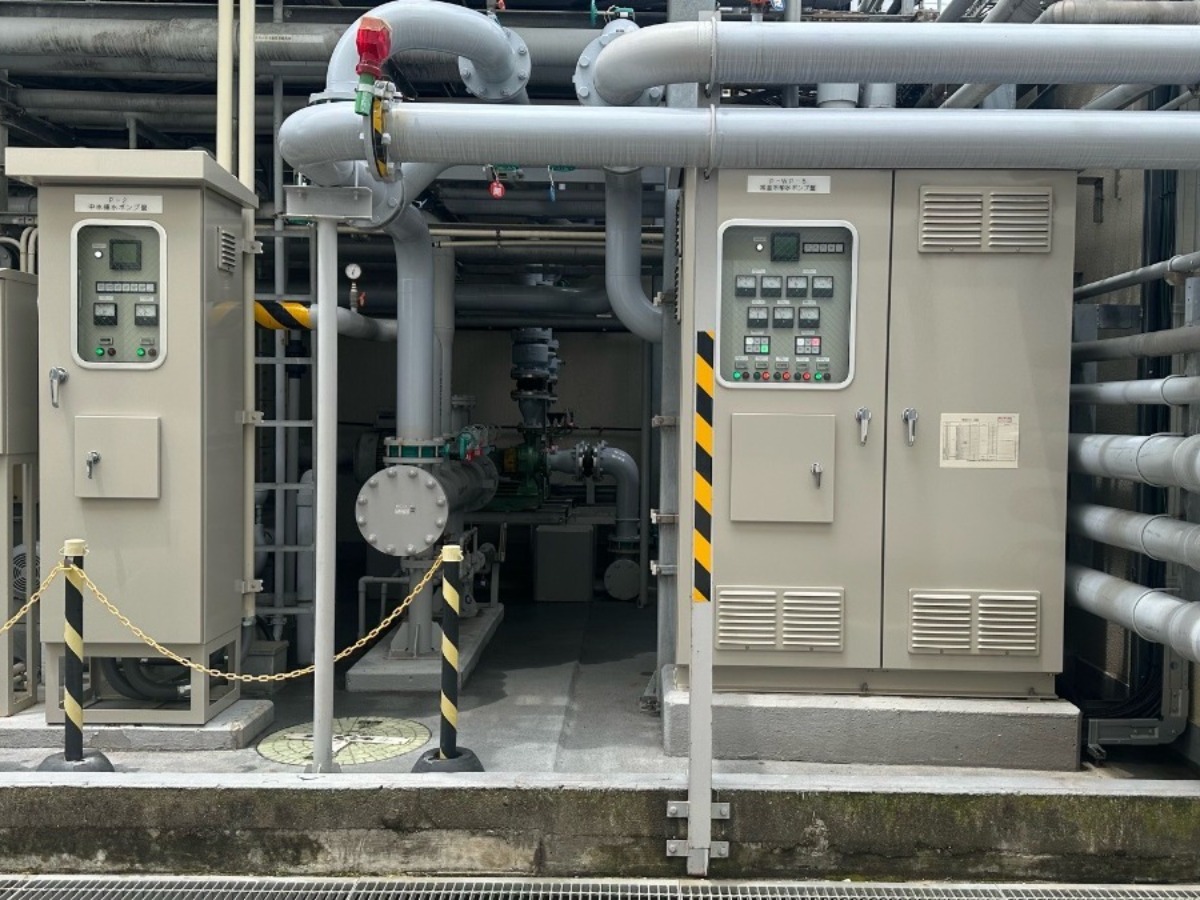
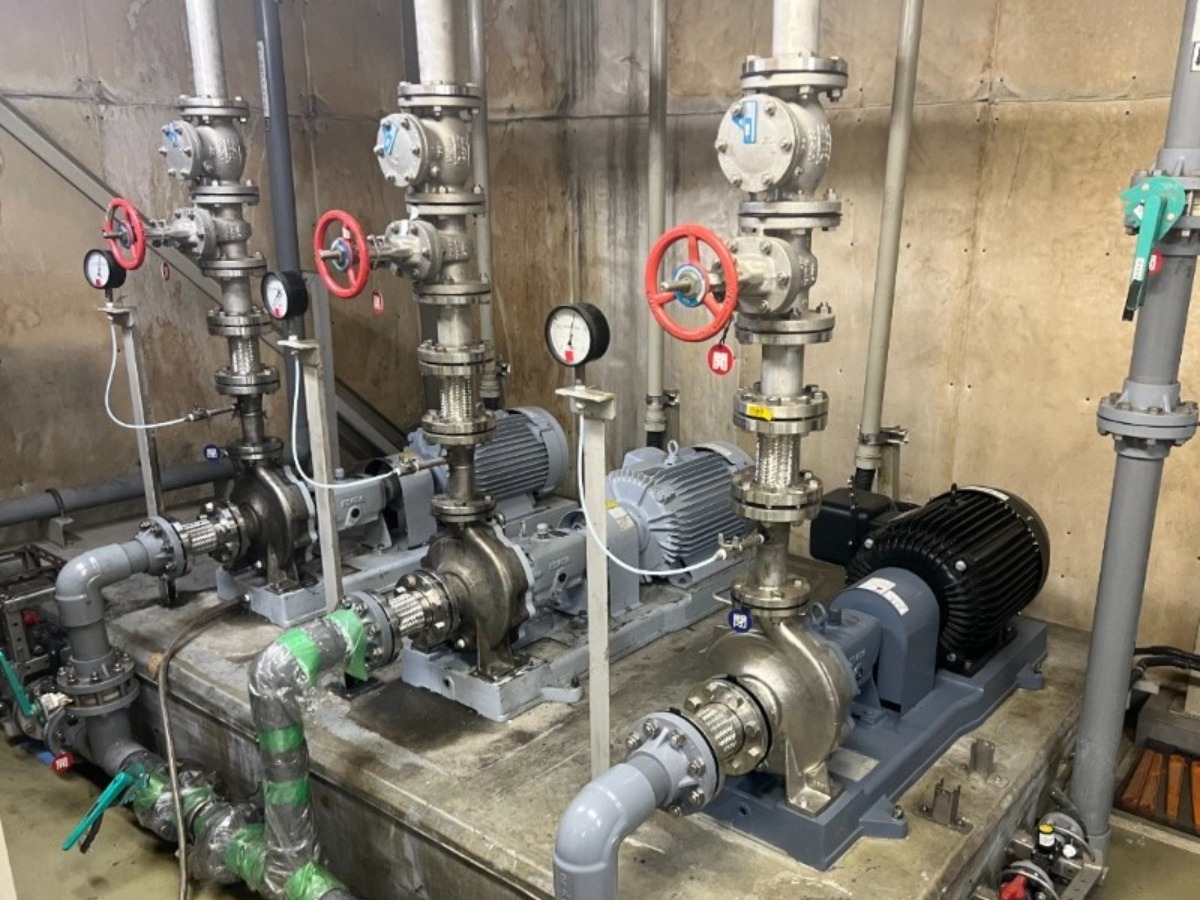
組立工程での省エネ対策
タイのNisshinbo Micro Devices は、IC(集積回路)1組立工程の真空発生システムの省エネ化として、中央真空ポンプを導入しました。
従来の小型真空ポンプ41台、真空エジェクター90台を高効率インバータ式中央真空ポンプ3台(通常運転としては2台を稼働)に更新することで、IC1組立工程の真空発生システムの省エネを実現しました。
2024年6月よりIC1組立工程に集中真空システムを導入したことにより、2024年度は半年間に606 MWh(温室効果ガス排出量:287 t-CO2)の削減を実現しました。
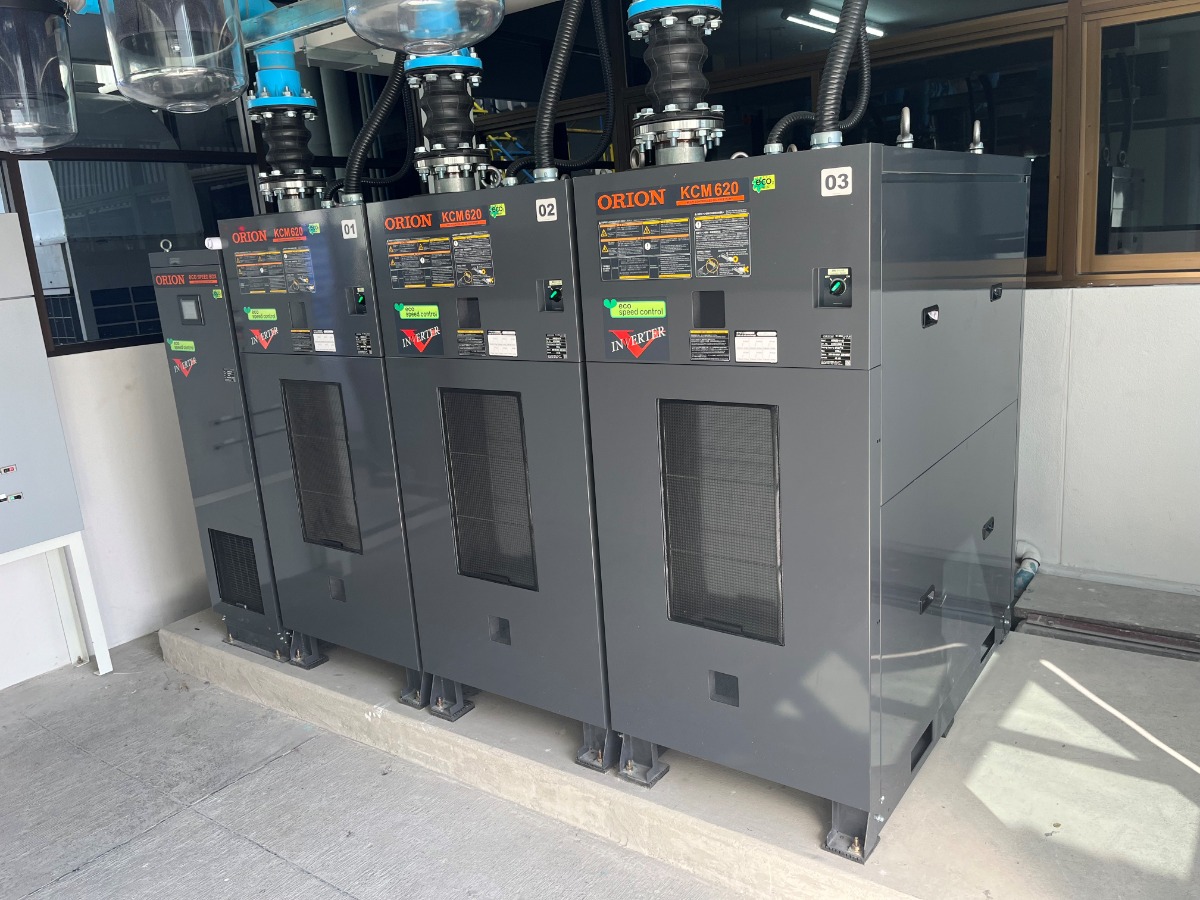
コンプレッサールーム改造による省エネ
韓国のSaeron Automotive Corporationでは、従来、冬期にあたる12~2月の夜間時間帯および、週末にコンプレッサールームを連続稼働してきました。
この従来の運営方式はエネルギー面では非効率的なものでしたが、設備保護に必要な措置として実施していました。コンプレッサールームの屋根構造物に設置されていた不要なダクトから、外部の冷たい空気が室内に流入し、コンプレッサー設備内の圧力センサーや配管などが凍結する恐れがあったためです。
この課題に対し、同社は外部からの冷たい空気の流入を遮断できるよう、不要なダクトを撤去する構造改善を行いました。また、コンプレッサーの内部配管およびセンサー凍結防止のため、まず油水分除去用フィルター設置を完了し、続いて圧力センサーの保温性能を強化しました。これにより、設備の凍結リスクを下げることができました。
今回のコンプレッサールームの改造により、不要なエネルギー消耗を減らし、冬場も安定した設備を維持できるようになりました。これからも省エネを実践できる活動を見つけて改善を続けます。
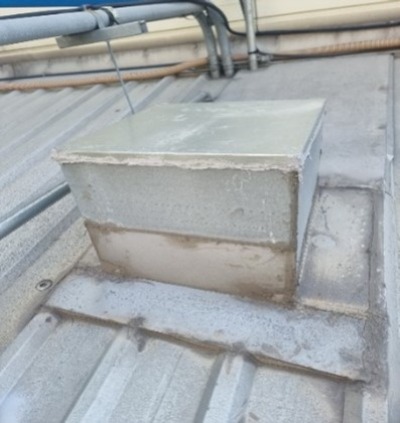
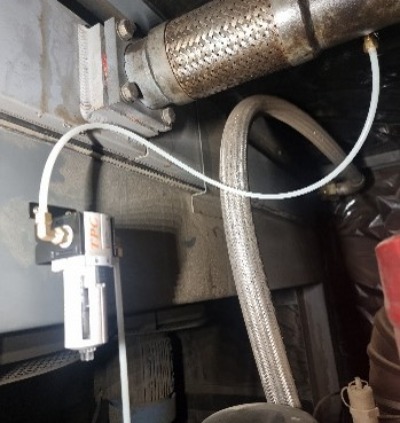
グループ全拠点の環境・省エネ横断活動
日清紡メカトロニクス(株)は、南部化成(株)をはじめとした海外を含めたグループ全拠点で、横断活動を月次で実施しています。当活動では、重点テーマを「温室効果ガス排出量削減にむけた省エネ活動」とし、温室効果ガス年間排出量1,000 t以上削減を目標に、課題策定、情報共有を行っています。
コンプレッサーの設定圧力の変更や照明のLED化など、グループ全拠点に共通する設備を中心に、省エネ活動を進めています。
加えて、施策事例をまとめた「省エネマニュアル」をグループ全拠点に展開しています。また、「省エネ勉強会」を開催し、グループ全拠点担当者の省エネに関する知識の拡充とスキルの向上、情報の共有を図りながら活動を推進しています。
これらの活動の結果、2024年度はグループ全拠点合計で、年間275件の省エネ施策を実施し、温室効果ガス排出量を年間1,084 t削減(電力使用量2,384 MWh/年削減)することができました。今後も、グループ全拠点で、省エネ・再エネ・電化などの施策を実行し、温室効果ガス削減活動を進めていきます。
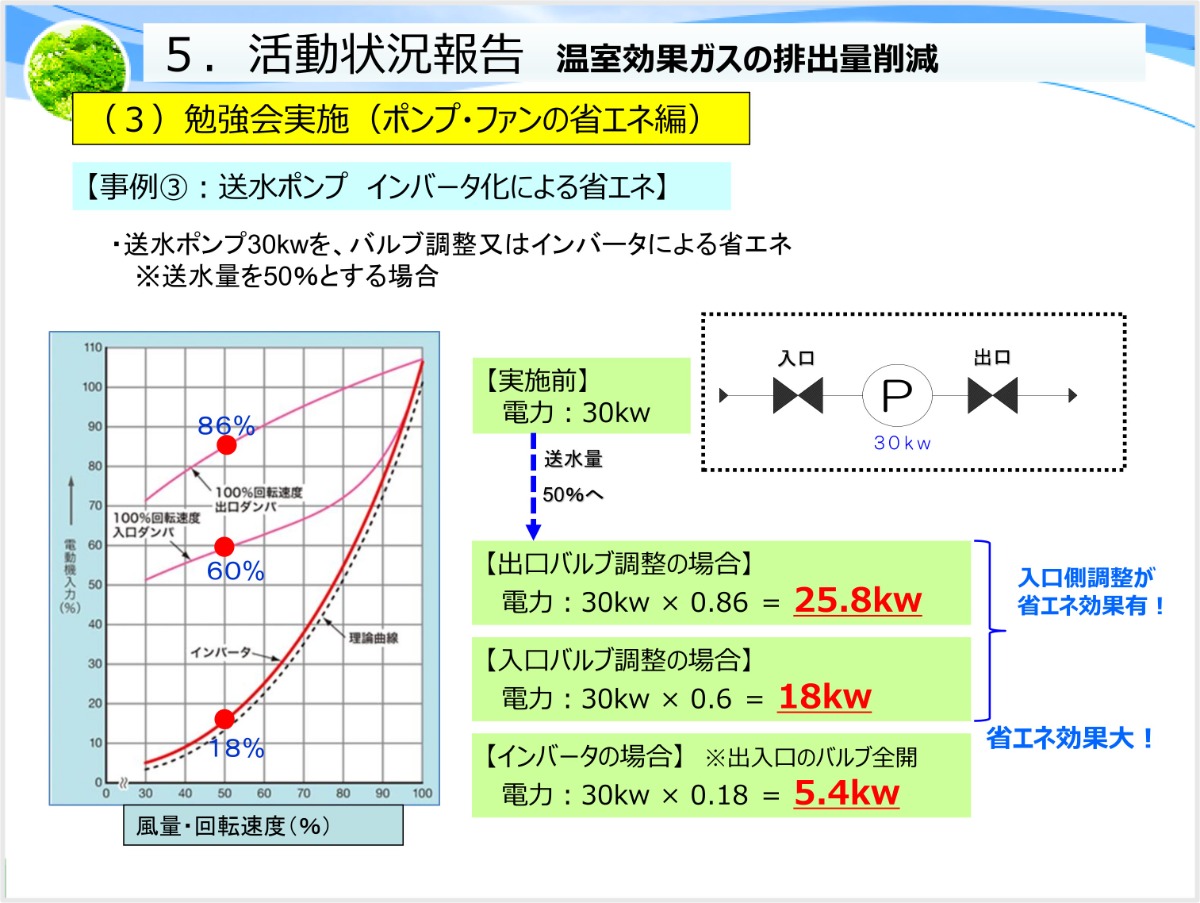
セントラルミストフィルター設備導入と加工区空調設備による省エネ
中国の日清紡大陸精密機械 (揚州) 有限公司では、中国国内における環境配慮への要求が年々厳しくなっていく状況下、従来から各加工機に設置していたミストコレクター設備の更新を進めています。
従来設備の更新にあたって、セントラルミストフィルター設備を設置することによりミストコレクター設備のフィルターをなくし、セントラルミストフィルター設備からVOCS設備の配管に接続して、直接排出するよう変更しました。これにより、2024年度は年間電気使用量を107.7 MWh削減しました。
また、同社の1工場加工区空調設備の省エネ改造更新により、省エネレベル3級から省エネレベル1級に変更しました。これにより、2024年度は年間電気使用量を526.9 MWh削減しました。
これらの取り組みにより、合計634.6 MWh/年(年間削減量304.6 t-CO2) の省エネ効果がありました。これからも、国内の環境配慮への要請に応えつつ、地球環境にやさしい工場運営を目指していきます。
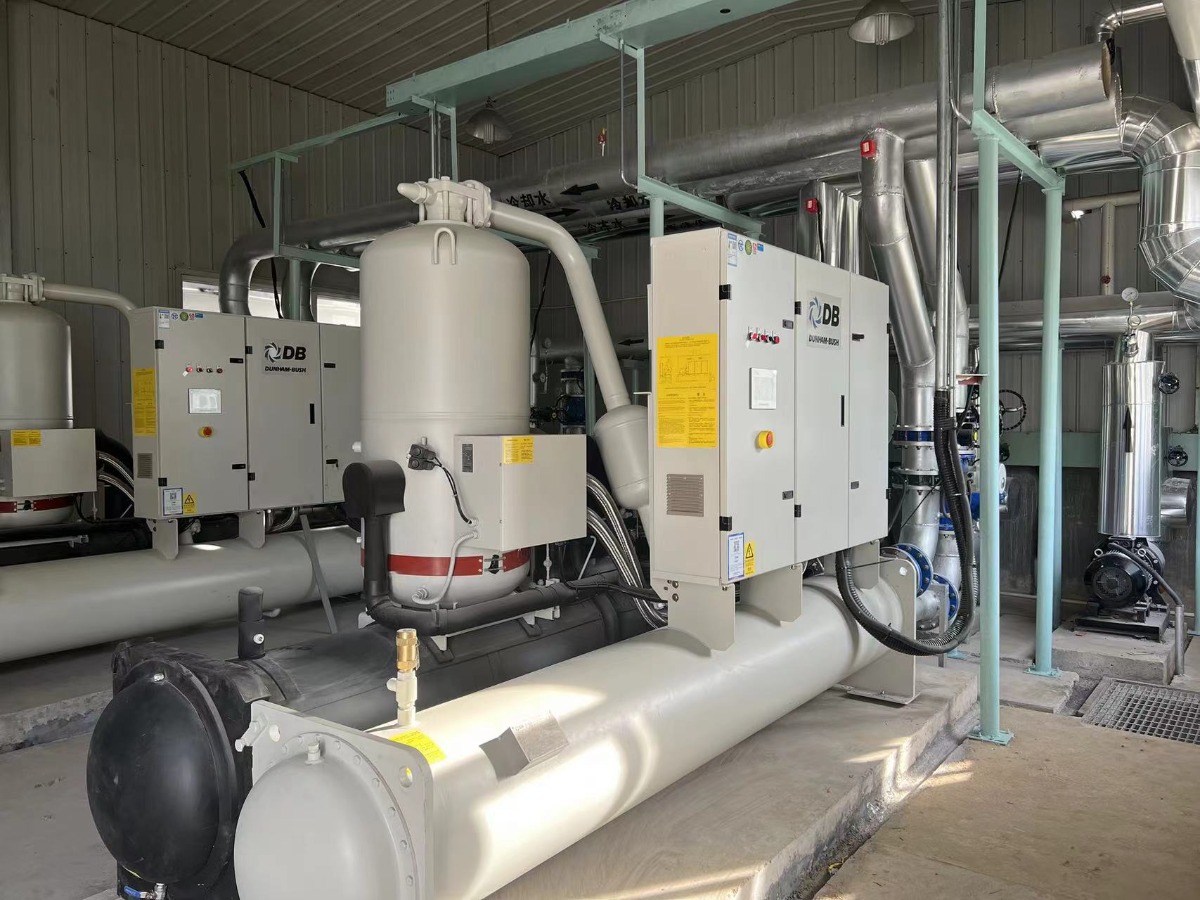
カイゼン活動によるエネルギー削減
日清紡ケミカル(株) 徳島事業所では、樹脂添加剤「カルボジライトⓇ」を製造しています。2024年度カイゼン活動において、「生産性向上・業務改善」のテーマのもと、「カルボジライトⓇ」の製造工程におけるエネルギー削減について活動を行いました。
油性製品の製造サイクルタイム短縮を検討し、1銘柄について冷却工程の終点温度を見直すことで、工程時間の短縮を図りました。2024年実績では、2.1MWhのエネルギー削減を達成しました。
「カルボジライトⓇ」製造後の製造設備洗浄では、洗浄溶剤を加熱し、所定時間を掛けて設備内の残留成分を溶解させた後に、洗浄溶剤を冷却する工程としています。従来、洗浄溶剤の加熱・冷却に多大なエネルギーを使用していました。
これに対し、カイゼン活動により、製品ごとに洗浄条件の最適化を行い、4銘柄で洗浄工程における洗浄溶剤の加熱・冷却を省略することや、10銘柄で洗浄工程の時間を短縮することができました。2024年度実績としては、前者では9.9 MWh、後者では0.9 MWhのエネルギー削減を達成しました。
さらに、製造設備内部を循環させる冷却液用ポンプの送液圧を下げてエネルギーを低減したことにより、2024年度実績で10.8 MWhの削減を達成しました。これらのカイゼン活動取り組みにより、2024年度は合計23.7 MWhのエネルギー削減を達成しました。