Basic Concept
The Nisshinbo Group's Business Conduct Guidelines states that "Safety is the Basis for Everything" and clearly states that the Group holds safety as the top priority for all of its activities to bring high-quality products to customers.
Promotion System
Nisshinbo Holdings Inc. reorganized its organizational structure in April 2025 to establish a Managing Officer system for each functional division with the aim of building and overseeing a structure that would lead to urgent change. Under a system in which the Managing Officer in charge of the Risk Management Department serves as the group coordinator, a Group Health and Safety Liaison Conference has been established to promote the prevention of occupational accidents and diseases throughout the entire Group. The Health & Safety Group of Nisshinbo Holdings Inc. serves as the secretariat for the committee.
The Nisshinbo Group's group coordinator reports on the status of achievement of the Group's targets and the occurrence of occupational accidents at the Board of Management*, and supervises the targets and their progress. The president of the Nisshinbo Group, who is the chief executive officer of the Group, conducts management reviews, and instructs necessary implementation measures for management, such as targets and priority policies for the following fiscal year. Special items are reported to the Board of Directors as appropriate.
* The Board of Management:Executive conference consisting of Directors, Executive officers, etc.
Please refer to "Promotion System for Sustainability Activity" for details regarding the organizational structure for promoting sustainability.
Specific Initiatives of the Nisshinbo Group
5th Sustainability Promotion Plan (to be achieved by FY2024)
In the 5th Sustainability Promotion Plan with FY2024 as the target year, the Nisshinbo Group set the following item as targets and KPIs to promote activities for occupational safety and health as a priority activity and achieve the goals of preventing occupational injuries.
The number of serious accidents "0".
The focus for FY2024 is on strengthening safety and health activities. The main specific initiatives are as follows.
-
① Prevention of serious accidents
When introducing new machinery, equipment, or chemicals, when significantly modifying existing equipment, and when significantly changing work methods, we will reduce the risk of occupational accidents through risk assessment. -
② Strengthening chemical substance management
Ensure the effective operation of exposure prevention equipment for hazardous chemical substances and the appropriate use of personal protective equipment at each workplace. -
③ Promotion of preventive measures against occupational accidents
Reduce occupational accidents caused by such work activities as falls and back pain by reviewing work methods and promoting health promotion activities.
As a result of these efforts, there were no major disasters during the three-year period covered by the 5th Sustainability Promotion Plan.
6th Sustainability Promotion Plan (to be achieved by FY2027)
In the 6th Sustainability Promotion Plan, which targets FY2027, the Nisshinbo Group will continue to focus on promoting activities for occupational safety and health as a priority initiative and will work to prevent occupational injuries. The Nisshinbo Group working toward the following goals through a PDCA cycle.
The number of serious accidents "0".
In FY2025, Nisshinbo will focus on improving safety and health management levels, preventing serious accidents, and providing education and training to employees to raise their awareness of safety and health.
Please refer to "Sustainability Promotion Plan and KPIs" for details regarding of the "Sustainability Promotion Plan and KPIs."
Occurrence of Occupational Injuries
In FY2024, the Nisshinbo Group had no serious occupational accidents (classified as grade 1 to7 death or disabilities).
The frequency rate of lost time injuries*, represents the frequency of occupational accidents, remained at 0.44 for the entire domestic group in fiscal 2023, the same level as the previous fiscal year, maintaining a favorable level compared to the domestic manufacturing industry.
When an occupational accident occurs, the person in charge of health and safety and the manager or supervisor of the department where the accident occurred conduct interviews the workers involved, including those affected, to determine the true cause and to implement measures to prevent a recurrence. In addition, the details of the occupational accident and countermeasures are compiled into a report and disseminated to all Nisshinbo Group companies to help prevent similar accidents.
* Frequency of injuries with lost work days: an index of the frequency of injuries with lost work days. Expressed as the number of work-related fatalities and injuries per 1 million total working hours.
Frequency of Injuries with Lost Work Days

Safety and Health Activities and 5S Activities
In addition to education at the time of hiring and at the time of changes in work content, each business site of the Nisshinbo Group strives to raise the safety awareness of each and every employee through small group activities and training to improve the abilities of employees engaged in safety and health work, hazard prediction training, 5S (Sorting, Setting-in-Order, Shining, Standardizing, Sustaining the Discipline) activities, and risk simulation education. Nisshinbo also formulates annual plans and systematically conducts risk assessments of equipment, operations, and chemical substances to determine priorities and implement preventive safety measures.
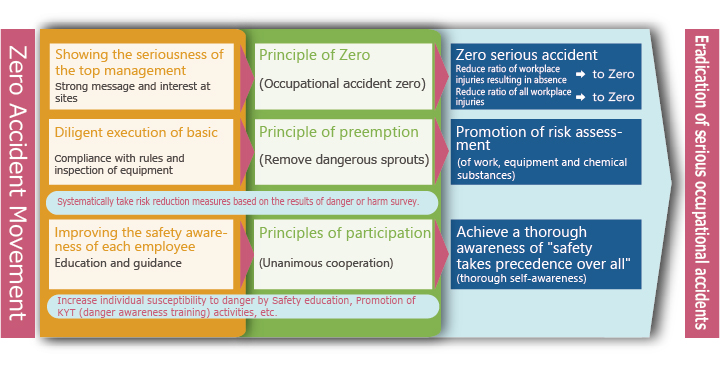
Health and Safety Education and Training
In accordance with the Nisshinbo Group's priority policy for FY2024, "Strengthening Safety and Health Activities," approximately 50 safety and health personnel from each business site participated in a study session to learn about efficient safety and health management operations and safety and health activities between business sites with a focus on the integration and collaboration of safety and health management operations through the integration of group companies.
The study session was held at Nisshinbo Micro Devices Inc., which, following the integration of business companies, began by understanding the differences in culture and approaches between each facility. The company then established monthly regular meetings with safety officers from all facilities to share information and strengthen safety and health activities. Participants exchanged opinions on these activities and challenges.
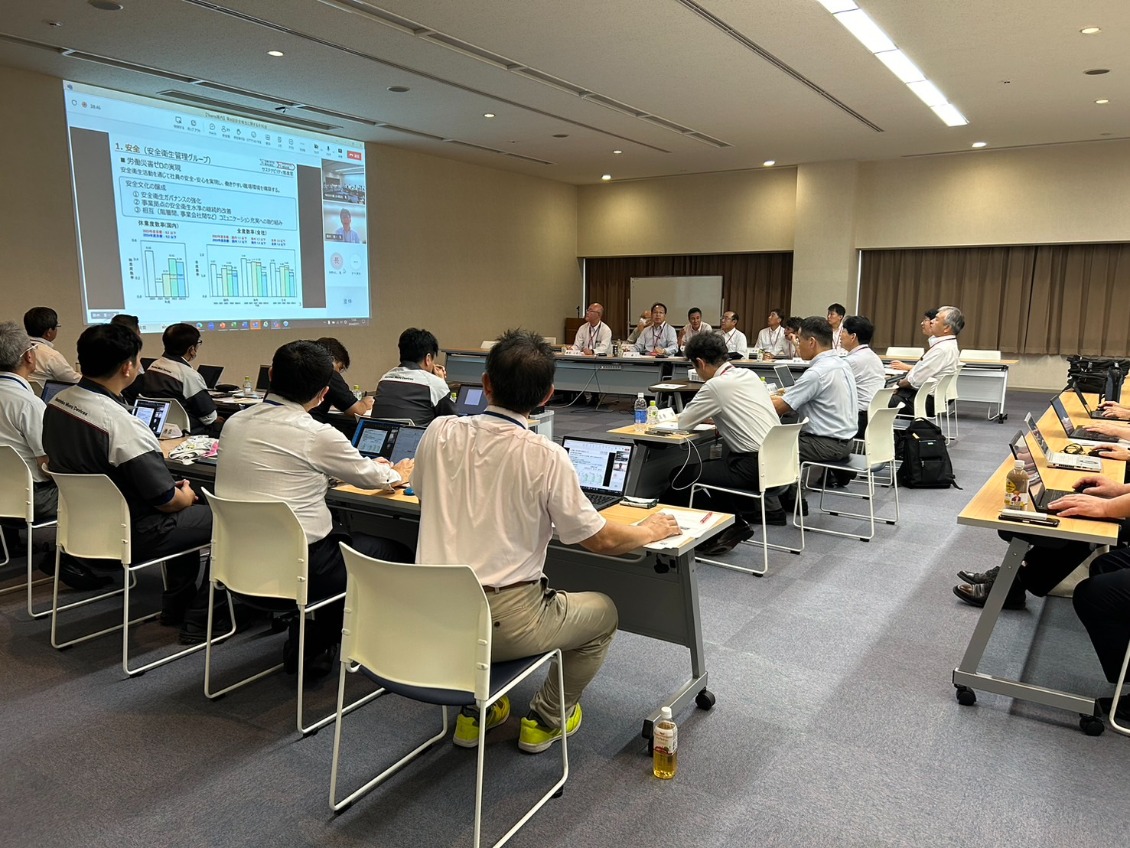
Safety and Health Audits
The Nisshinbo Group periodically audits the status of health and safety management at each business site by organizing an audit team consisting of the Health & Safety Group of Nisshinbo Holdings Inc., the labor union, health and safety managers representing operating companies, and health and safety managers from other business sites. In FY2024, Nisshinbo conducted health and safety audits at 45 business sites in Japan, mainly manufacturing sites, and 5 overseas business sites.
At the end of the fiscal year, the monitoring team prepare a comprehensive audit report based on these audit results. The team also share accident risk analysis results and case studies of excellent activities throughout the Group and incorporate them into occupational safety and health activities in the following fiscal year.
Chemical Substance Management Initiatives
From 2023, autonomous management of chemical substances has been required because of the revision of government ordinances related to the Industrial Safety and Health Act. Based on this, Nisshinbo confirmed the status of compliance with the Guidelines for Chemical Substance Management in the Workplace formulated in collaboration with experts from domestic group companies through safety and health audits. The Group also held review meetings with the departments in charge at domestic group companies to resolve issues and problems at each workplace, thereby improving the level of chemical substance management.
Activities at Business Sites in Overseas
Overseas group companies strive to raise the awareness of safety by each employee through the implementation of danger-detection training and danger-perception training provided at each site in cooperation with the core companies under its jurisdiction in accordance with the Guidelines for Behavior with the "Safety is the Basis for Everything." In addition, the Nisshinbo Group works to prevent the recurrence of occupational injuries at sites within the Group companies and to prevent similar injuries. Regarding the chemical substances handled, the Group continue to disseminate the danger and thoroughly implement the use of personal protective equipment to prevent health problems.
Specific Activities of the Group Companies
Promotion of traffic safety activities
Japan Radio Co., Ltd. Nagano Plant and Nagano Japan Radio Co., Ltd. have been designated "Model Workplaces for Promoting Traffic Safety in Fiscal Year 2024" by the Nagano Prefectural Police. Together with the Nagano South Police Station and the local traffic safety association, they will engage in traffic safety awareness activities in the vicinity of their workplace for one year (April to December)
Many employees commute to work by car or bicycle, and traffic accidents occur every year at intersections and crosswalks around the company premises. With the aim of raising traffic safety awareness among all employees and preventing accidents, employees participated in activities to promote traffic safety.
Specifically, in June, July, and September 2024, the companies conducted awareness campaigns by stationing staff at the main gates of their business premises, surrounding employee parking lots, and intersections, and provided traffic safety education (car and bicycle simulators, physical ability tests, etc.). In December, the companies invited a police officer to give a lecture on traffic safety for drivers and cyclists, which was recorded and made available as an e-learning course at the end of the fiscal year during the accident-free week (mandatory for all employees).
The companies asked participants to fill out a questionnaire after viewing the video, in which they pledged to observe traffic safety, in order to raise awareness of traffic safety.
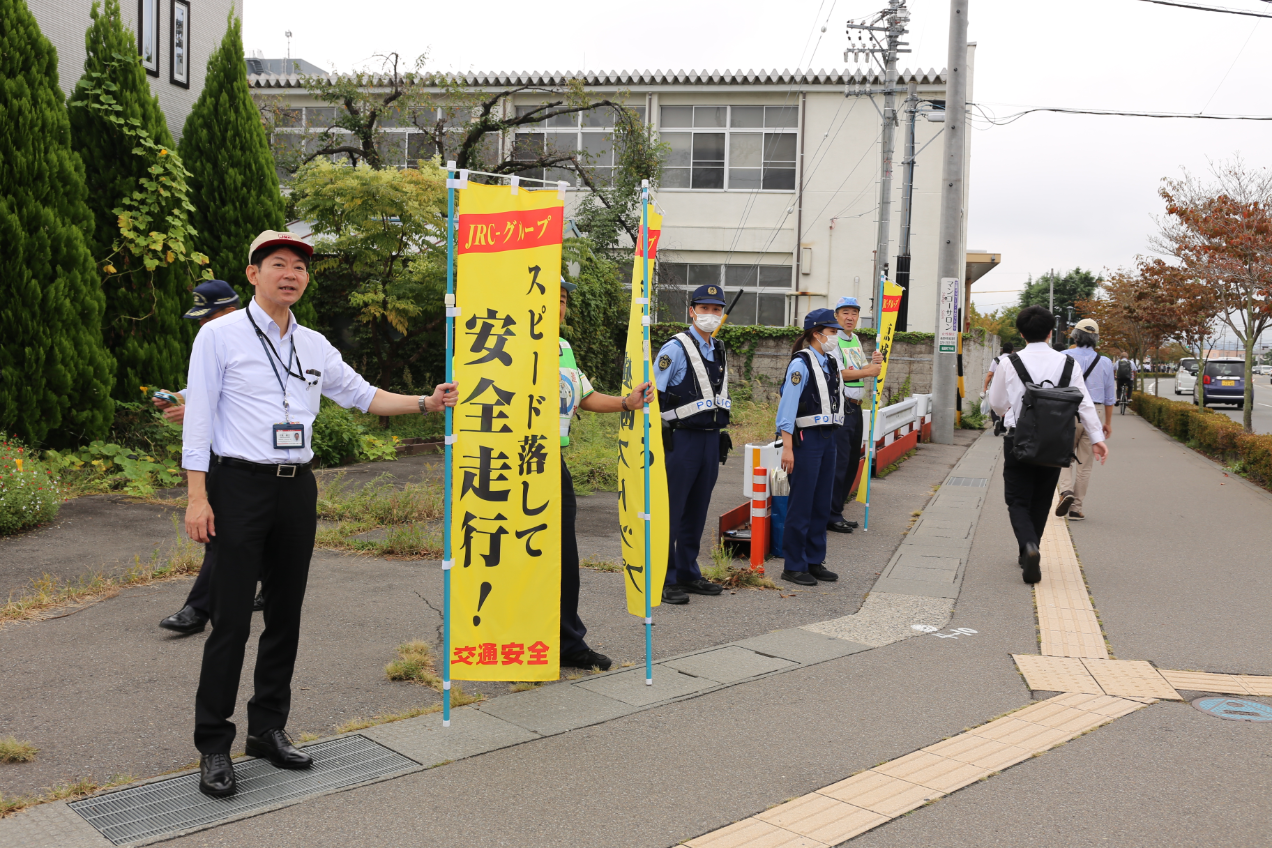
Efforts to prevent falls
Falls account for 70% of workplace accidents and are considered to be particularly serious, often resulting in fractures and prolonged absences from work. At Japan Radio Group, falls occur from slipping on frozen surfaces, mis-stepping on stairs, and tripping over steps or carts.
In light of these circumstances, Japan Radio Co., Ltd. implemented an e-learning program "Preventing Falling Accidents" (mandatory for all employees) in conjunction with Safety Week in July 2024. The company conducted educational activities to implement measures to prevent falls, including typical patterns of falls (slips, trips, and missteps), thorough implementation of the so-called 4S principles (sorting, straightening, sweeping, and cleaning), allowing sufficient time, taking small steps, avoiding work under conditions where the ground is not visible, selecting appropriate footwear for the task and weather conditions, and posting signs in areas of the workplace where falls are likely to occur.
In addition, at the Nagano and Kawagoe Plants, with the aim of preventing falls on stairs, senior employees conduct monthly guidance on the use of handrails with a target retention rate of 90%. The results are reported at the monthly safety and health committee meeting with a breakdown by building.
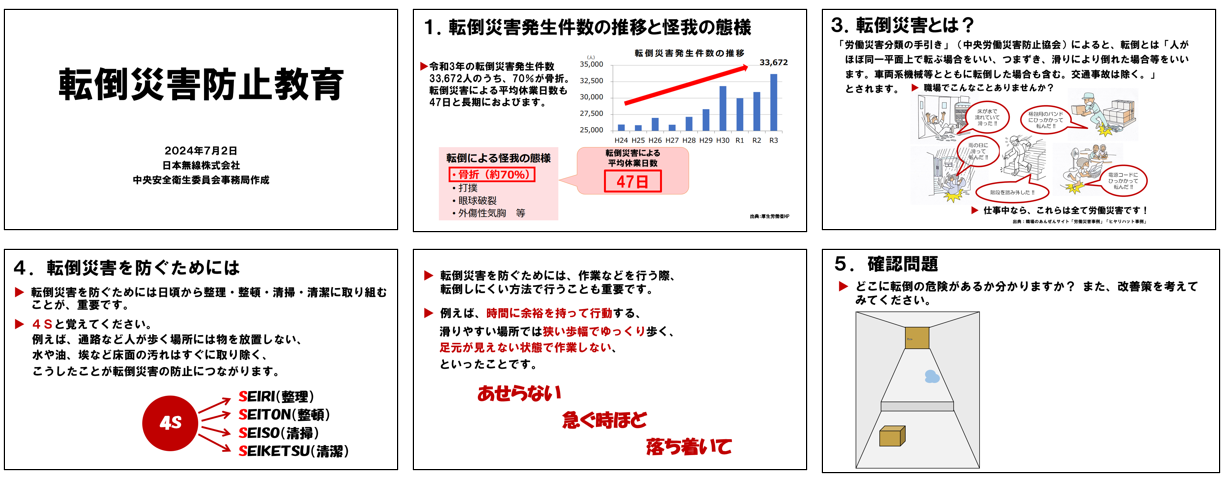
Traffic Safety Activities and Labor Standards Bureau Director's Award
HYS Engineering Service Inc. and GOYO ELECTRONICS CO., LTD. introduced the DRIVE CHART into their company vehicles. An AI-powered drive recorder constantly analyzes driving behavior to identify and detect risky driving actions that could lead to accidents. The system aims to improve carelessness and driving habits that lead to traffic accidents, thereby efficiently reducing accidents. Specifically, it detects risky driving behaviors (such as sudden acceleration, sudden steering, and distracted driving) by individual drivers and provides feedback to the drivers to correct improper driving habits and reduce accidents.
HYS Engineering Service Inc. is primarily engaged in the maintenance of communication and video systems and owns 108 company vehicles for use in visiting customer sites. Approximately 200 employees, or about 30% of the total workforce, are registered to drive company vehicles, and the company vehicles collectively drives approximately 120,000 km per month. Driving a car always carries the risk of accidents, but to reduce that risk, the company introduced the DRIVE CHART, which detects risky driving behavior and records video footage. Managers are notified in real time, which helps reduce the risk of accidents.
In addition, at the safe driving competition held in FY2024, drivers formed small groups and considered the measures necessary for safe driving by sharing their ideas with each other.
As a result of these efforts, HYS Engineering Service Inc. achieved zero traffic accidents in 2024. In addition, the company was recognized for its particularly outstanding traffic accident prevention measures, which serve as a model for others, and received the Tachikawa Labor Standards Inspection Office Director's Award for Excellent Workplaces in Occupational Safety and Health in November 2024.
GOYO ELECTRONICS CO.,LTD. participated in the DRIVE CHART Traffic Safety Campaign 2024 jointly organized by companies that adopted DRIVE CHART in the spring of 2024. The company implemented e-learning for all employees and publicly announced the results of risk driving monitoring within the company during the campaign period to raise awareness of safe driving.
The DRIVE CHART Award 2024, which recognizes companies committed to reducing accidents, announced the top 10 companies with the lowest number of risky driving incidents per 1,000 km driven as the DRIVE CHART STARS (General Vehicle Category).
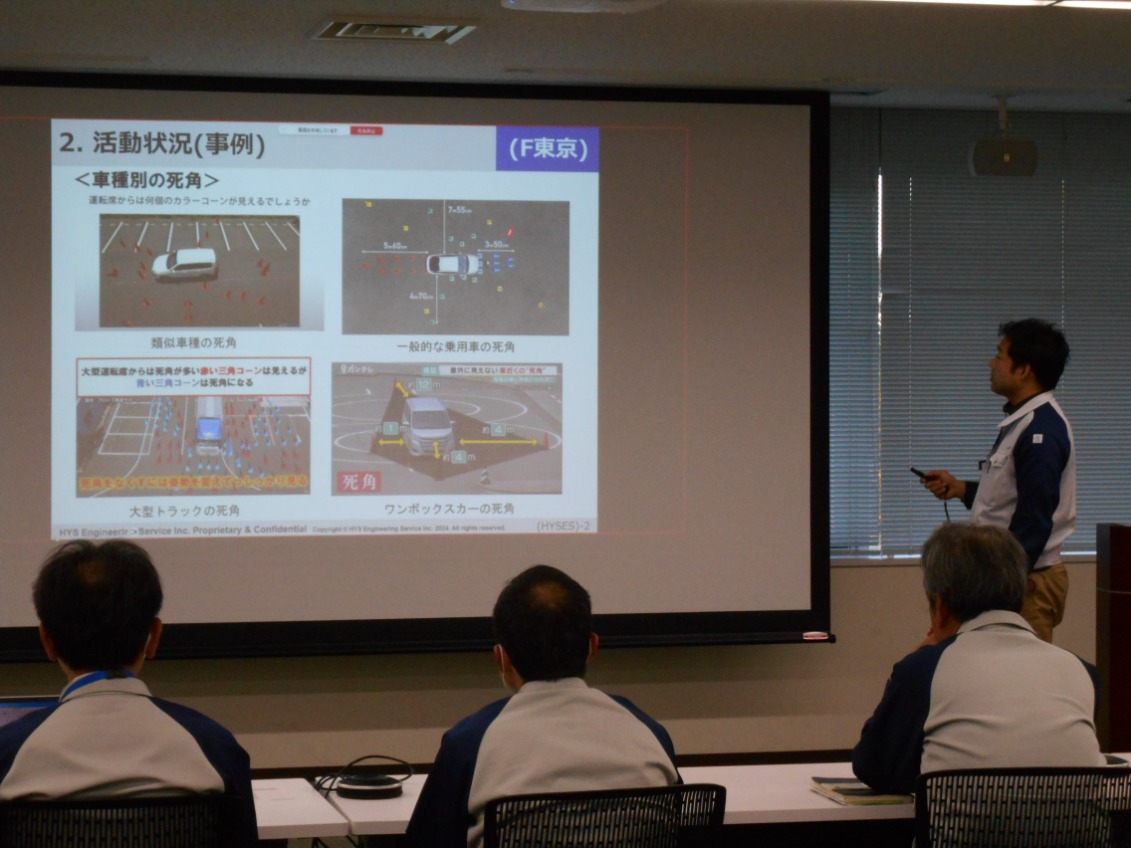
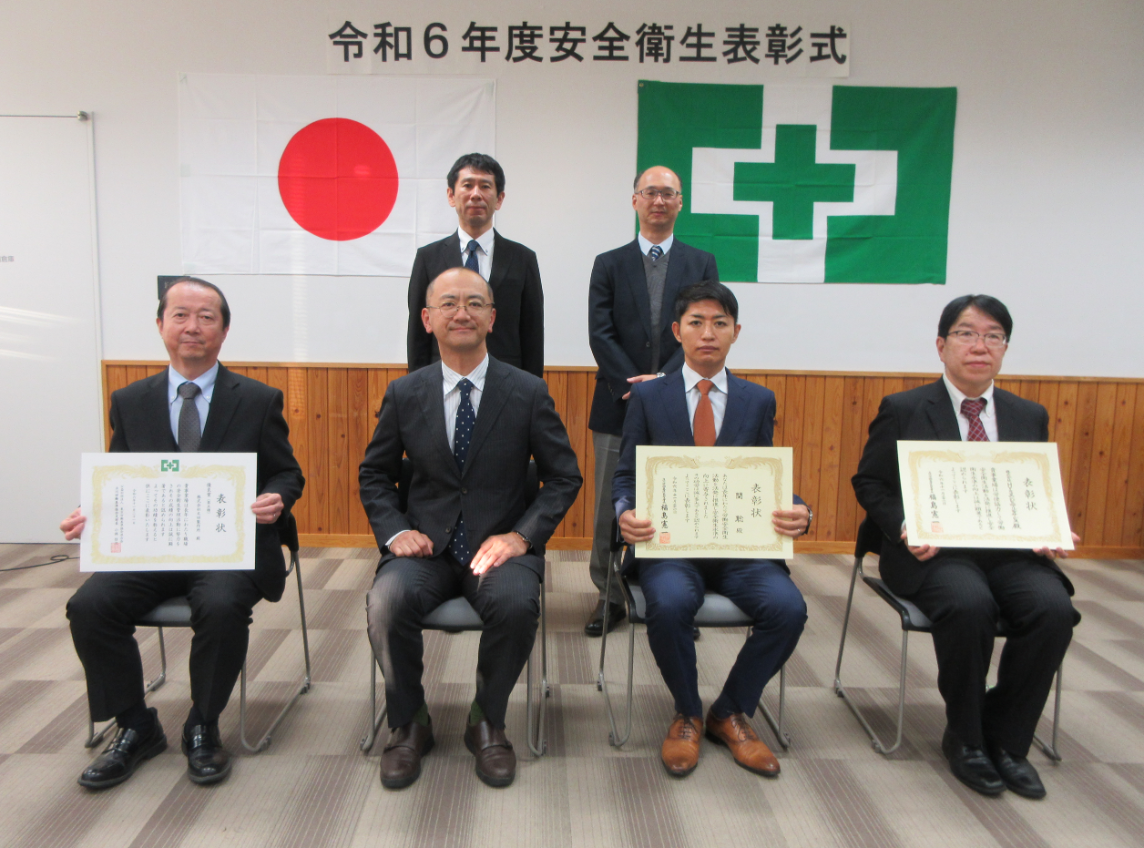
Received the National Award for Excellence in Safety and Health
Nisshinbo Micro Devices (Thailand) Co., Ltd., in September 2024, was take part in "Contest on Workplaces of Excellence in OSH" in Thailand. The first contest was launched in 1986, as an important part of the National Safety Week event.
The company has been honorably awarded the 2024 excellent practices establishment on occupational safety and health national level as the 21th year of achievement. Nisshinbo Micro Devices (Thailand) was evaluated for its high level of safety awareness among all employees, from management to staff, and its numerous safety activities.
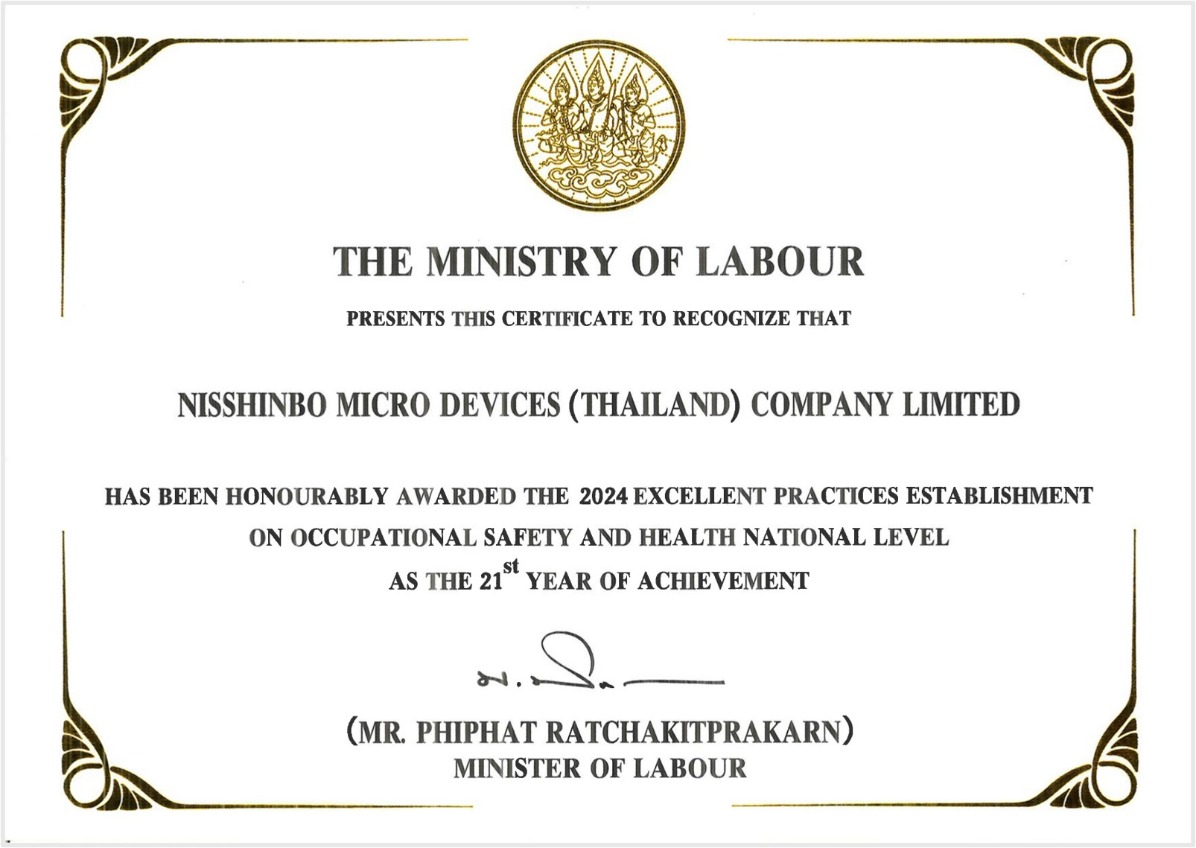
Danger Prediction Training Short Video Contest
Nisshinbo Micro Devices (Thailand) Co., Ltd. conducted safety week activities in August 2024. During this event, all employees signed the safety declaration sheets posted in the cafeteria and enjoyed games related to safety signs and traffic safety to raise the awareness of safety.
In addition, the company held an internal contest featuring short videos of the hazard prediction training (KYT) conducted at the start of each workday. The submitted short videos showed creativity in the use of call phrases and pointing gestures, and many videos conveyed a sense of unity within the departments. The activity was also an opportunity to learn about KYT events in other departments that employees do not usually see, so it was a good reminder to be more aware of hazard prediction.
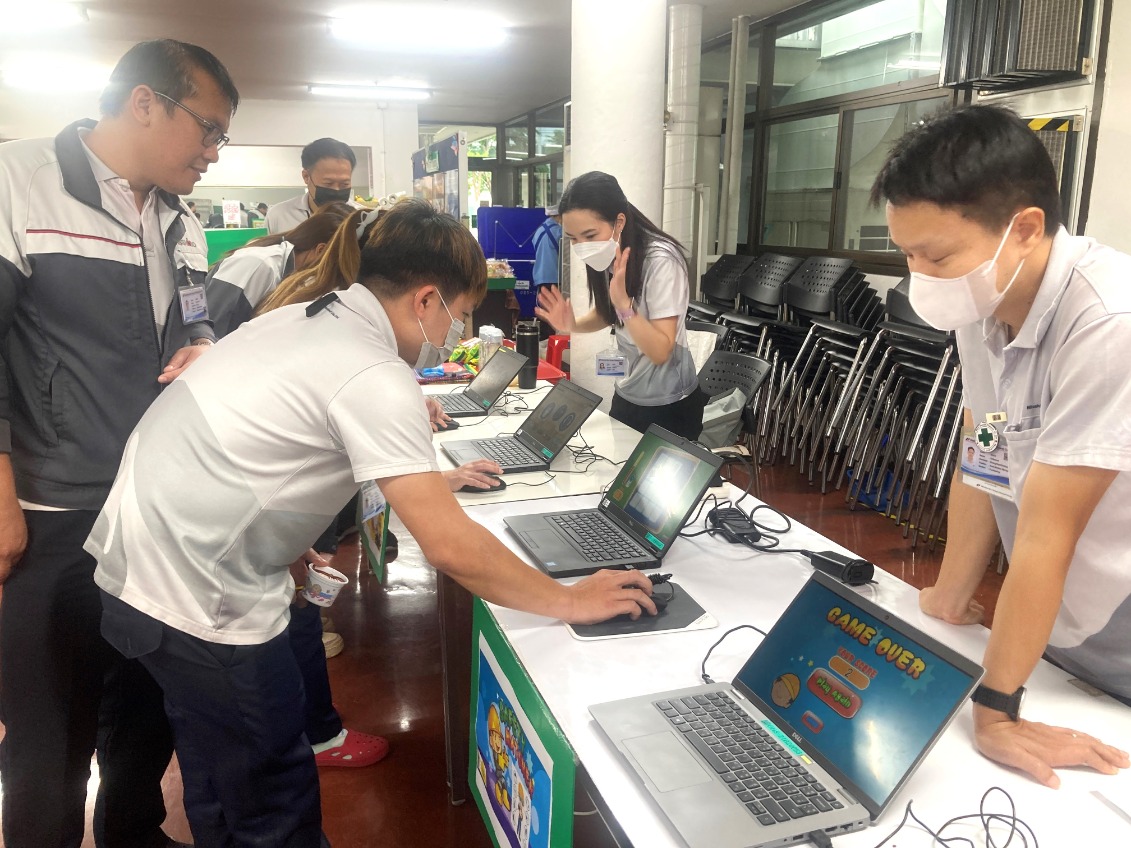
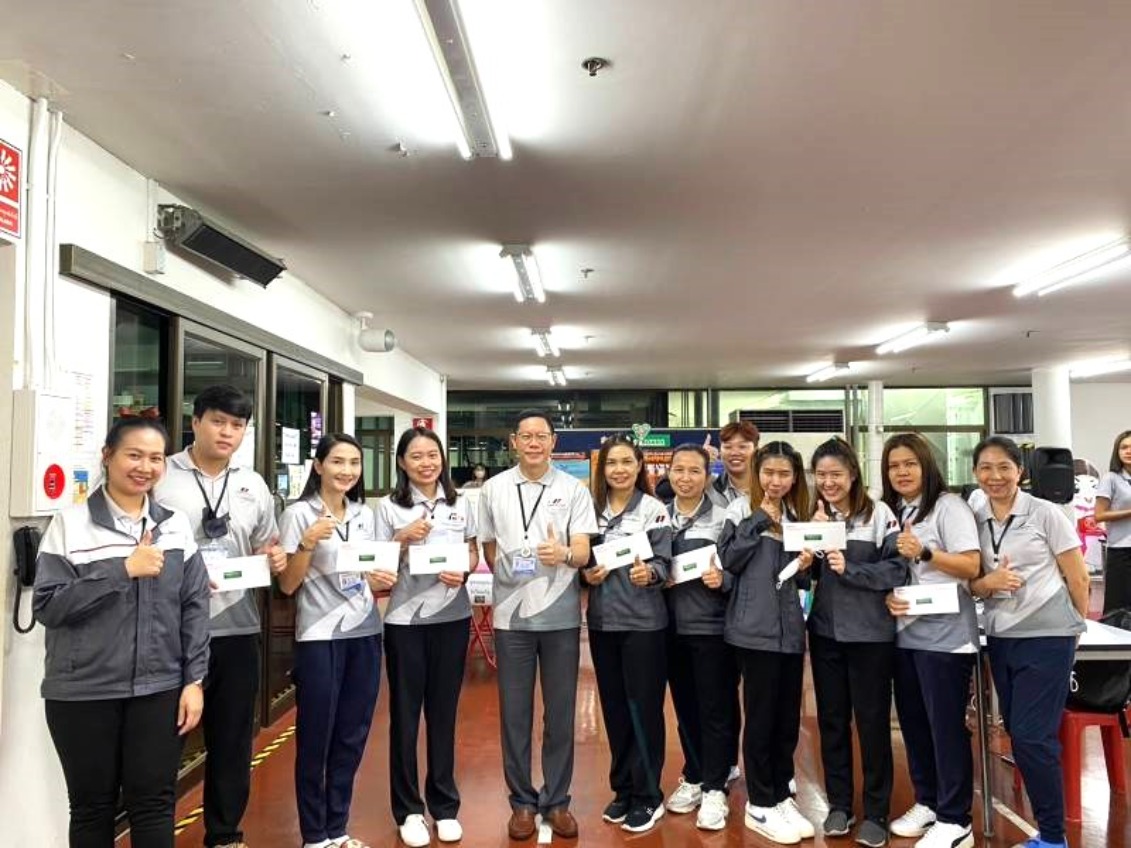
Promotion of safety and health activities
At Nisshinbo Mechatronics(Shanghai)Co., Ltd. the company established a Safety and Health Committee composed of five subcommittees (Risk Assessment, Traffic Safety, 5S, Near Miss, and KYT (Hazard prediction ("Kiken Yochi") training) ) and an office, and Nisshinbo Mechatronics(Shanghai)Co., Ltd. is implementing safety and health activities. In addition to activities within each subcommittee, the company sponksors safety conferences and 5S conferences with the participation of all employees to enhance safety awareness among everyone at the company.
At the Safety Conference, the company conducts surveys on understanding and safety awareness after the conference and provides individual follow-up as necessary. At the 5S Conference, each workplace reports on the results of improvements made to hazardous areas in their workplaces. In addition, the EHS* Management Department conducts hazard awareness training for all employees using devices that simulate hazards, such as entanglement and electric shock.
In addition, the company conducts monthly safety inspections by management and provides opportunities to hear reports on improvement initiatives voluntarily implemented by each workplace, such as improvements to difficult work areas. The company also established a system that allows employees to easily report any hazards they discover in the workplace using smartphones. In FY2024, the company received 277 reports, demonstrating that this has become an established safety and health activity in which all employees participate.
* EHS: An acronym for Environment, Health, and Safety. It refers to environmental and occupational safety and health.
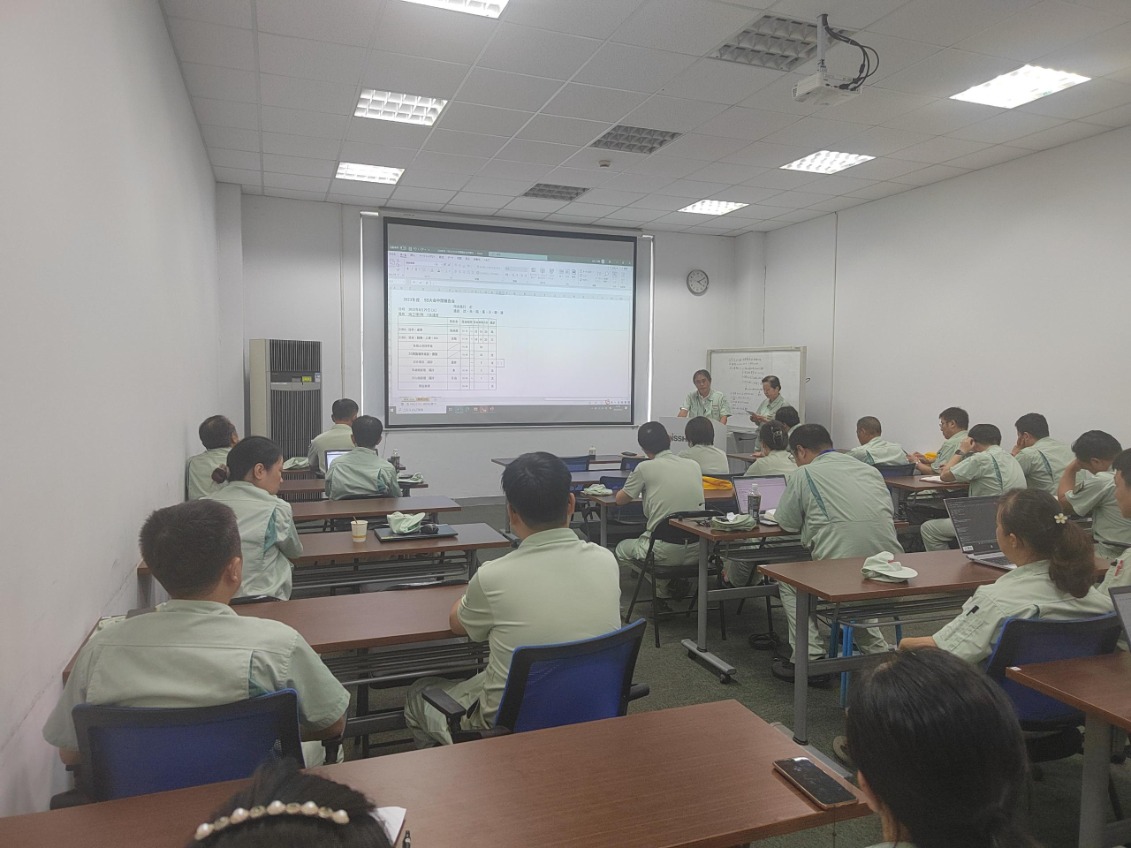
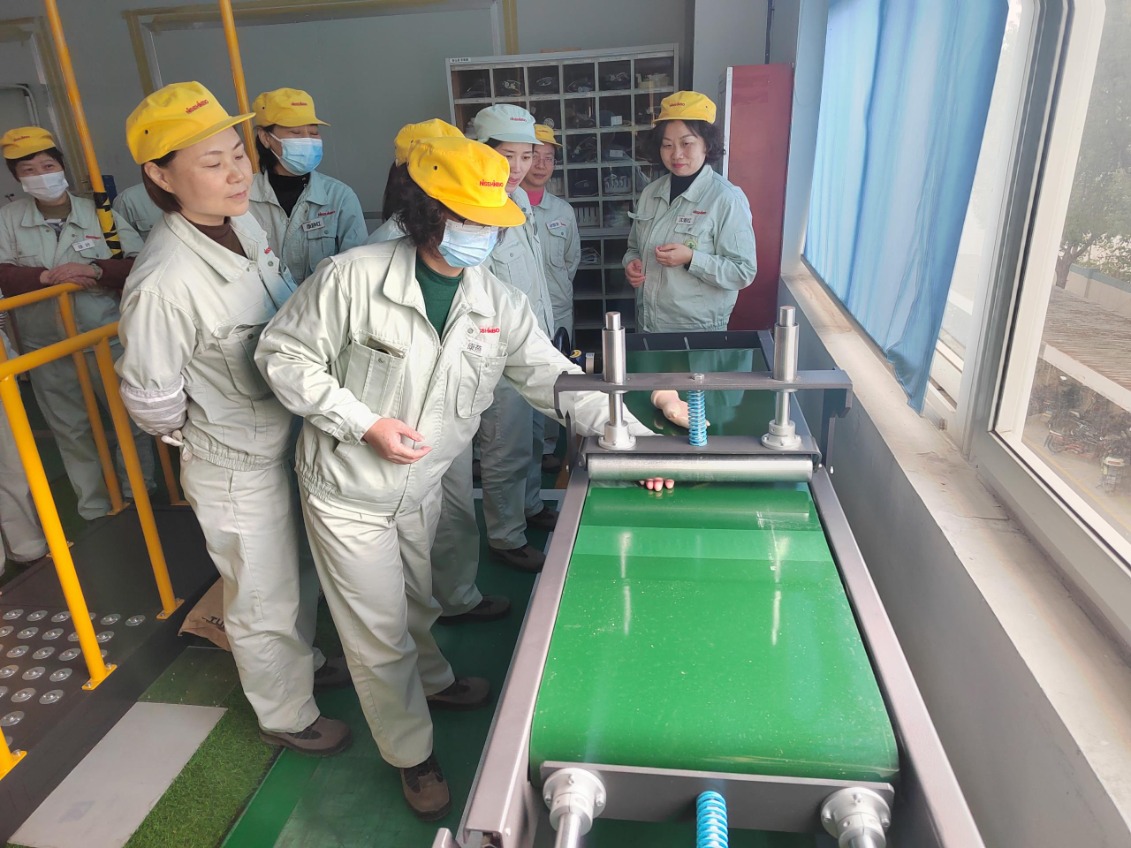
Strengthening chemical substance management
Nisshinbo Chemical Inc. has conducted monthly meetings since 2024 to promote cooperation among safety managers and chemical substance managers at each business site, manage progress in responding to revisions to the relevant laws and regulations, resolve issues arising in chemical substance management, and share information.
For FY2024, Nisshinbo Chemical Inc. revised the internal regulations regarding chemical risk assessment (CRA) and unified the methods for conducting CRA and the approach to risk levels, which had previously been handled separately by each workplace. Additionally, the company conducted chemical substance-related education for employees handling chemical substances using e-learning materials provided by the Ministry of Health, Labour and Welfare. This education covered such topics as hazards and toxicity, pictograms, proper use of protective equipment, and labeling with the aim of ensuring that employees acquire the necessary knowledge to protect themselves.
In order to confirm the level of knowledge retention, a test to assess understanding was conducted at the end of the training. For areas where comprehension was lacking, the company provided follow-up training and provided feedback on the content of the next training session, striving to continuously maintain and improve the level of chemical substance management among employees.
Safety awareness promotion
Nisshinbo Do Brasil Industria Textil LTDA. conducts training sessions led by factory safety engineers with the aim of raising employee safety awareness. The sessions are held four times a year and are mandatory for all employees at the supervisor level and above. Supervisors who participate in the sessions are also responsible for conveying the information to subordinates. The content of the sessions is reviewed each time by the Safety Office in accordance with the current situation at the factory.
In FY2024, in light of the large number of commuting accidents that occurred in the previous year, the company conducted training on traffic safety. In addition, Nisshinbo Do Brasil Industria Textil LTDA. provided training on human rights and disseminated the results of analyses of industrial accidents that occurred at factories in the past, along with points to note.
In FY2025, in response to requests from senior managers who expressed a desire to learn how to interact with and supervise their subordinates, the company plans to hold a training session led by a legal advisor.
As part of its safety awareness activities, the company shows videos in the cafeteria that are based on the monthly safety goals. These videos are created each month by factory safety engineers. They use simple pictures and large text to ensure that the message sticks even when viewed while eating, and the content is kept simple.
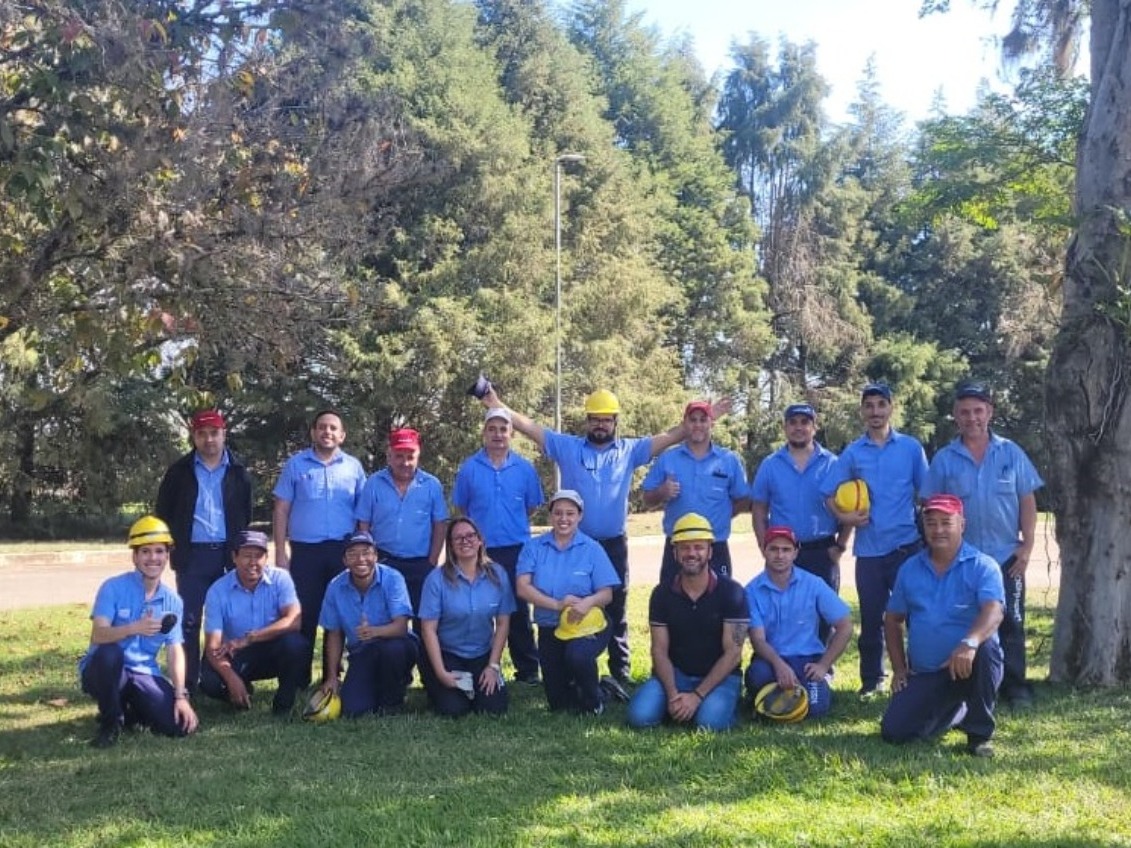