Basic Concept
The Nisshinbo Group's Business Conduct Guidelines include Awareness and Concern towards its environmental impact. The Group promotes water conservation, recycling, and other activities with an eye to improving the quality of resource recycling, and faithfully realizes a safe and secure society for all people. The Group manages key performance indicators (KPIs) as part of systematic measures to achieve its environmental target regarding reducing water consumption per unit of sales.
【Main measures】
- ① Promoting water conservation activities through ISO 14001 activities
- ② Expanding activities such as the introduction of water-saving equipment at manufacturing sites, reduction of water consumption and reuse of treated wastewater
- ③ Efforts toward sustainable water intake at overseas sites with different water availability conditions, such as use of rainwater and water recycling (returning to groundwater)
- ④ Activities in the Textiles business to purify well water that has been drained and deliver a portion of it to neighboring residents free of charge
- ⑤ Contributing to Japan and overseas wastewater treatment fields by providing microbial carriers for water treatment in the Chemicals business
Please refer to "Promotion System" in "Environmental Management" for the promotion system.
Specific Initiatives of The Nisshinbo Group
Use of Water Resources
The Nisshinbo Group's actual water use in FY2023 was 6,240 thousand m3, the same as the previous year. The volume of water used per sale was 11.8 m3 per million yen, a 2% reduction in the volume of water used per sale in the previous year. Water consumption per net sales has been decreasing year by year because of the progress of water-saving activities, such as the replacement of water-cooled air conditioners with air-cooled ones in the Wireless and Communications business.
The volume of water recycled was 840 thousand m3 in FY2023. This was a decrease of 13% in the recycling volume of water in the previous year. In the Textiles business, production of spunlace* (water-jet interlacing method) nonwoven fabrics, which use a large amount of water, decreased, and the amount of water reused in air conditioning facilities also declined.
* Spunlace: A production method for nonwoven fabrics in which fibers are intertwined by high-pressure water flow.
Water Usage and Water Usage per Unit of Sales
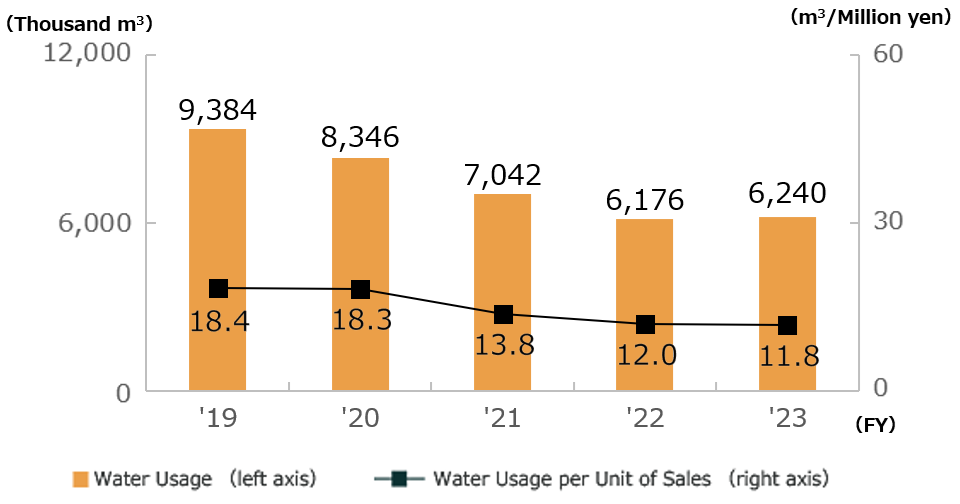
*1 Because of the transfer of all shares of TMD FRICTION GROUP S.A. (TMD), a subsidiary in the Automobile Brakes business, on November 30, 2023, and for other factors, TMD and 21 other companies were excluded from the scope of consolidation. Therefore, TMD and 21 other companies are included in the data until November 2023.
*2 On December 27, 2023, HVJ Holdings, Inc. and its subsidiary Hitachi Kokusai Electric Inc. and 7 other companies were included in the scope of consolidation, but are not included in the data for FY2023.
Trends of Water Recycled
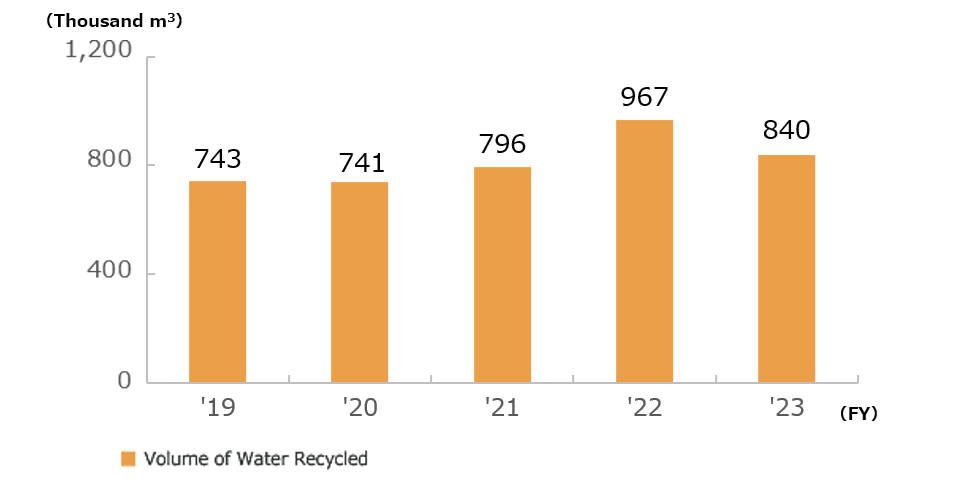
*1 Because of the transfer of all shares of TMD FRICTION GROUP S.A. (TMD), a subsidiary in the Automobile Brakes business, on November 30, 2023, and for other factors, TMD and 21 other companies were excluded from the scope of consolidation. Therefore, TMD and 21 other companies are included in the data until November 2023.
*2 On December 27, 2023, HVJ Holdings, Inc. and its subsidiary Hitachi Kokusai Electric Inc. and 7 other companies were included in the scope of consolidation, but are not included in the data for FY2023.
Trends in Volume of Water Usage by Business
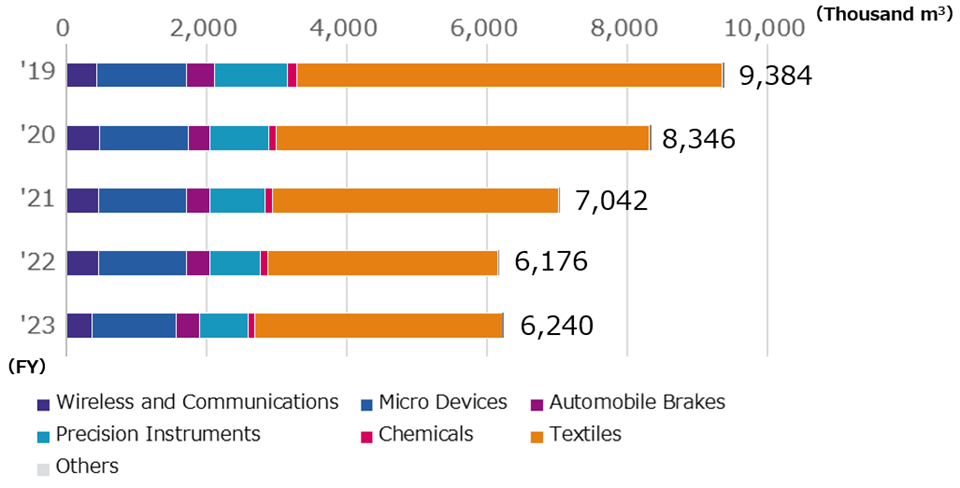
*1 Because of the transfer of all shares of TMD FRICTION GROUP S.A. (TMD), a subsidiary in the Automobile Brakes business, on November 30, 2023, and for other factors, TMD and 21 other companies were excluded from the scope of consolidation. Therefore, TMD and 21 other companies are included in the data until November 2023.
*2 On December 27, 2023, HVJ Holdings, Inc. and its subsidiary Hitachi Kokusai Electric Inc. and 7 other companies were included in the scope of consolidation, but are not included in the data for FY2023.
Understanding and Monitoring Water Risks
The Nisshinbo Group conducts water risk assessments of all of the Group's business sites and main supply chains using the AQUEDUCT Water Risk Atlas* published by the World Resources Institute (WRI).
As a result of the AQUEDUCT assessment, six of the Group's business sites (Nisshinbo Mechatronics India Private
Limited in India, Saeron Automotive (Beijing) Co., Ltd. and Saeron Automotive (Yantai) Co., Ltd. in China, and PT.
Nikawa Textile Industry, PT. Nisshinbo Indonesia and PT. Naigai Shirts Indonesia in Indonesia) are classified as
"Extremely high" areas. At view point of the current water consumption at these sites, the Group estimates that it
is not highly likely to have a significant impact on its business activities.
In addition, 11 sites of its main supply chain companies (Indonesian, Cambodian and Chinese suppliers in Textiles business, and Chinese suppliers, etc. in Automobile Brakes business) are classified as "Extremely high" areas.The Group continues to monitor the situation of those sites and supply chains that have been assessed as "Extremely high."
The Group has also assessed the risk from flooding as of 2050 in its climate change scenario analysis. The Group will promote risk reduction measures to deal with property damage and loss of business due to possible flooding.
* AQUEDUCT Water Risk Atlas: Maps based on 12 different water risk indicators, including "physical water stress," "water quality," "water resource regulatory risks," and "reputational risks."
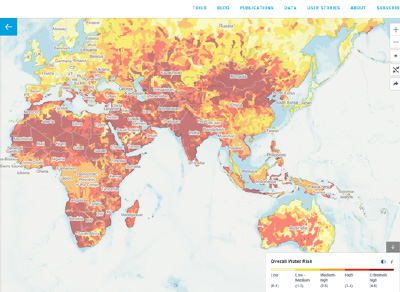
CDP Water Security 2023 Evaluation
The CDP is an international NGO working in the environmental field. The CDP surveys more than 23,000 companies worldwide, assigning scores from A to D and more than 1,100 cities, states, and regions to assess how CDP effectively responds to issues such as climate change, deforestation, and water security. The Nisshinbo Group received a "B-" rating in Water Security 2023.
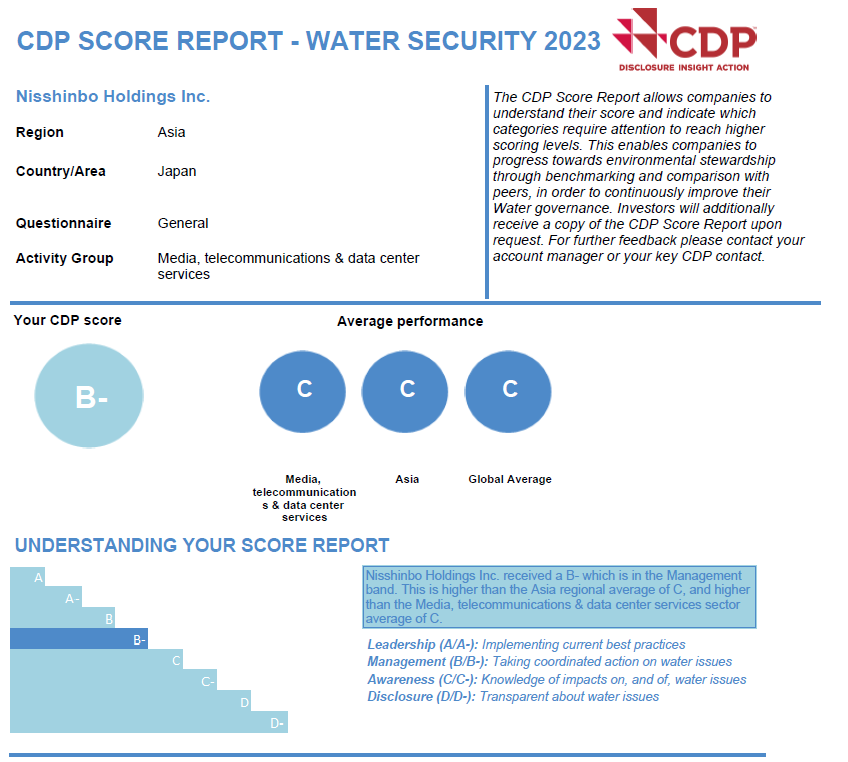
Specific Activities of the Group Companies
Reduction of Groundwater Use
Nagano Japan Radio Co., Ltd. has been working to reduce groundwater consumption by switching from water-cooled to air-cooled air conditioners when updating air conditioners since 2014.
The company's annual groundwater consumption in FY2022 was 315,000 m3, but after 18 units were renewed in FY2023, groundwater consumption in FY2023 was approximately 204,000 m3, a reduction of approximately 35% (111,000 m3) compared to FY2022. The company is planning to renew five units in FY2024.
The company will continue to reduce groundwater consumption by upgrading from water-cooled to air-cooled air conditioners.
Effective Use of Well Water by Indirect Cooling Water Recovery
Nisshinbo Micro Device Inc. Kawagoe Plant worked to reduce water consumption by establishing a circulation system to recover and reuse indirect cooling water for production facilities.
In the past, in systems where quality requirements were not so high, the water used as indirect cooling water for production facilities was drained from the water tank of groundwater (well water), which was the raw water for the pure water used for wafer cleaning. By returning this drained water to the water tank, circulating it, and reusing it, the company has reduced the amount of wastewater to zero. As a result of this initiative, from October to December 2023, the company was able to reduce pumping volume by 11,000 m3. For the current fiscal year, the company expects to achieve an annualized reduction of approximately 44,000 m3.
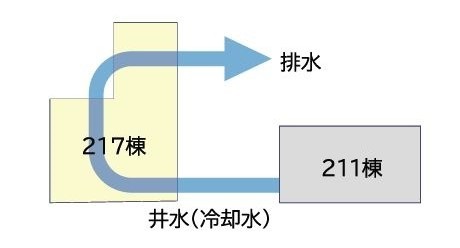
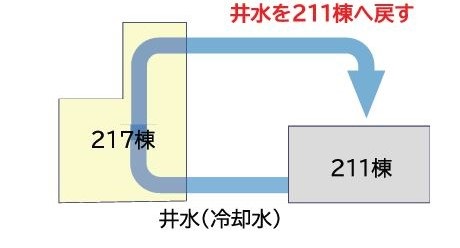
Wastewater Reuse System (MRO) Enters Its 15th Year of Operation
Nisshinbo Micro Devices Fukuoka Co., Ltd. has been using a wastewater reuse system (MRO) device that uses reverse osmosis membranes for the purpose of reusing sewage since FY2009. The system collects and treats a portion of the sewage effluent and uses it for power equipment (cooling towers, scrubber supply water, etc.), and will be in its 15th year of operation in 2024.
The production volume of wastewater MRO decreased by approximately 12,000 m3 (1.3%) from the previous year because of the shutdown of wastewater MRO equipment operations (+ five days compared to the previous year) following adjustments for reduced production from August to December (+ eight days shutdown compared to the previous year). However, approximately 85,000 m3/year of sewage water was reused throughout the year.
The facility operates 24 hours a day, and in addition to regular maintenance (membrane replacement, water sampling analysis, and maintenance) based on maintenance contracts, the appropriate operating conditions are maintained by adjusting and controlling the amount of the different chemicals added to cope with changes in raw water quality. In addition, data is collected to manage and monitor operating conditions. The company will continue to perform planned periodic maintenance and strive for stable operation while continuing to study future increases in processing capacity.
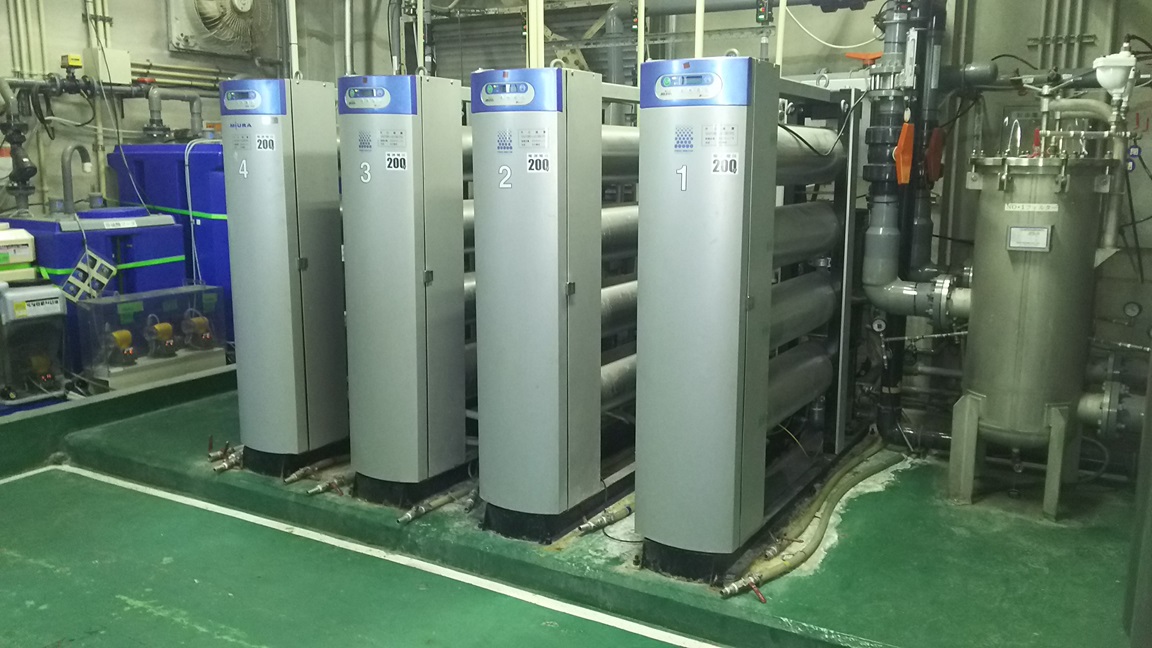
Reduction of Industrial Water Consumption by Reusing Treated Wastewater
Nisshinbo Somboon Automotive Co., Ltd. in Thailand is reusing treated wastewater from its wastewater treatment system as cleaning water for a wet scrubber that cleans exhaust gases generated by local exhaust ventilation systems as well as water for green areas within the plant. This is intended to reduce the amount of industrial water used.
The wastewater treatment system uses a biological membrane treatment system (ACTICONTACT ), a treatment method using aerobic organisms with a special carrier called Actilite to which bacteria are attached.
The wet scrubber is a standard type consisting of a filler, shower, and mist separator. Periodic measurements of exhaust gases are also taken to ensure that the exhaust treatment is functioning properly. The reuse of this treated wastewater has resulted in an annual reduction of approximately 3,000 m3 of industrial water consumption. This is equivalent to approximately 30% of the industrial water used in a year.
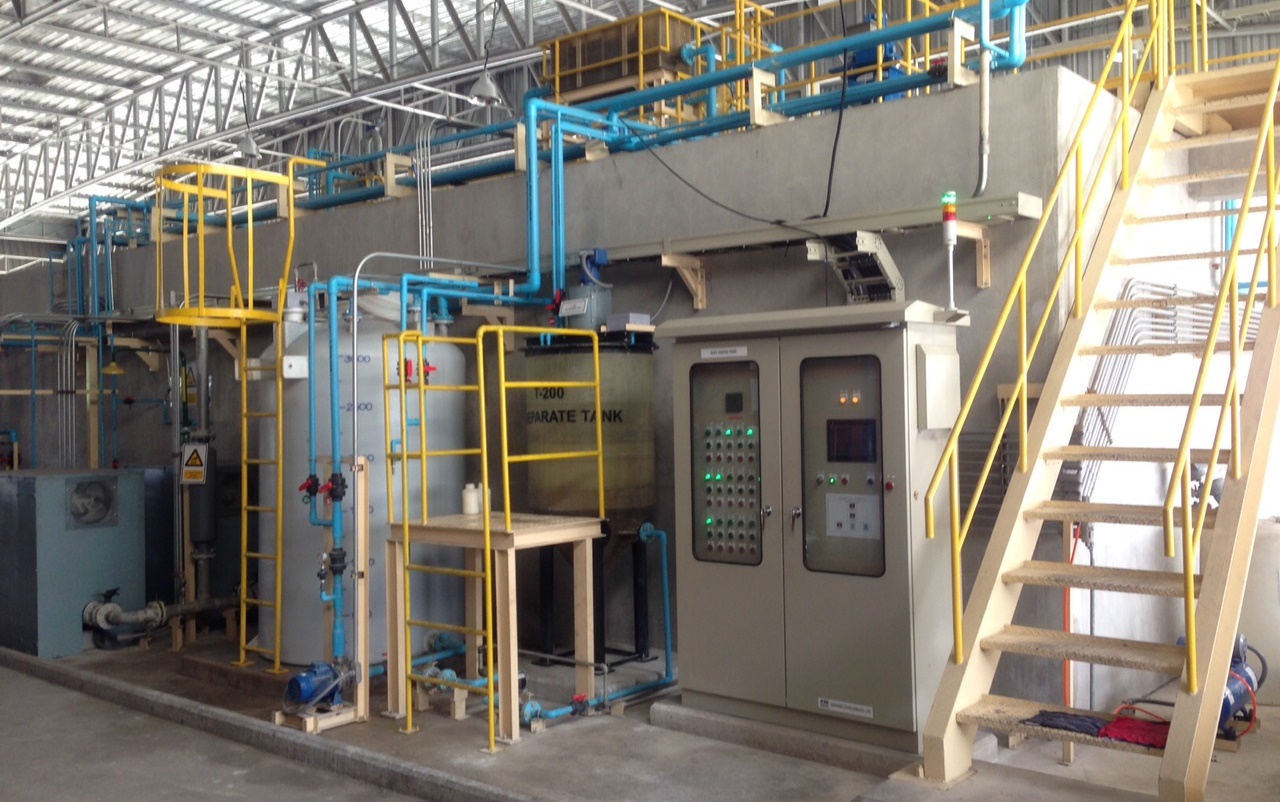
Reduction of Water Consumption by Recovering Boiler Cooling Water
Nisshinbo Saeron (Changshu) Automotive Co., Ltd. in China uses a single gas boiler to supply steam for the sewage treatment facility and humidifying steam for the plant during the fall and winter seasons. The boiler steam cooling water is discharged to an external sewage treatment plant via the plant's drainage channel.
For heat recovery and water reuse, the company commissioned a boiler manufacturer to retrofit the plant in 2023, adding one additional cooling water warming tank, 38 meters of collection pipe, and one water supply pump. Cooling water self-flows through the piping to a heat-retention tank, and water is returned to the boiler through a pump for reuse. The quality of the cooling water is relatively good, enabling stable recovery and reuse of water while meeting the usage demand of the boiler and reducing wastewater volume by 1,200 m3 per year.
The heat recovery process also reduces the use of city gas fuel, which saves 12,000 m3 of gas fuel per year, or 23 t-CO2 per year in terms of CO2 emissions.
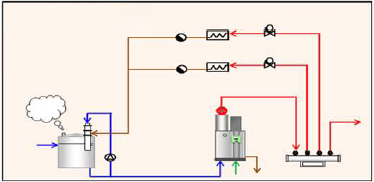
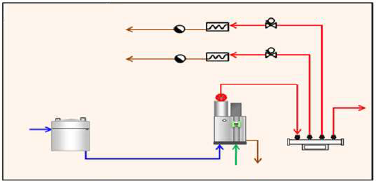
Reduction of RO Water Usage
Nisshinbo-Continental Precision Machining (Yangzhou) Co., Ltd. in China examined the possibility of saving energy and reducing resource use under the circumstance that environmental requirements in China are becoming stricter each year, provided that it does not affect equipment capacity and product quality. The company uses a lot of water throughout the year in its plants, so the idea of reducing water use came up as a suggestion. Therefore, the company considered the balance between quality impact and resource use reduction, and by reducing the number of backwashes of the high-pressure washer (HPW), the company was able to save 1,707 m3 of hazardous waste water discharge and RO water usage per year.
Before reduction: RO water consumption 14,300 m3 (actual in 2022)
After reduction: RO water consumption 12,600 m3 (actual in 2023)
Reduction details: Annual tap water consumption = 1,707/70% = 2,400 m3 (RO water purification ratio 70%:
30%)
Reduction of Water Consumption by Changing Air Compressor Operation Method
Nisshinbo Chemical Inc. Tokushima Plant was equipped with air compressors as utility equipment with two 22 kW water-cooled inverter type compressors in main alternating operation and one 7.5 kW air-cooled on/off type compressor in standby operation. The main operation of air-cooled compressors is effective in reducing water consumption, but the challenge was how to keep the water-cooled inverter type on standby.
First, to establish the conditions under which the air-cooled system would be used as the main operation, the company surveyed the air consumption of each manufacturing facility and established a manufacturing facility operation pattern that would allow stable air supply at 7.5 kW with the air-cooled system.
Next, to put the water-cooled compressor on standby, the company changed each set pressure and sequence control of the water-cooled compressor, so that even in the unlikely event that the air-cooled 7.5 kW compressor could no longer feed air stably, and the water-cooled compressor would start up only when necessary. As a result of the above, filtered water consumption relative to production volume in FY2023 was reduced by 2.6 m3/t compared to FY2022 and by 2,200 m3 in FY2023 actual.
Initiatives to Reduce Water Consumption
Nisshinbo Textile Inc. uses running water to cool crushers and extruders in the elastomer production process. Automatic valves were installed on the frequently-operated units, and ball valves were installed on the infrequently operated units to reduce usage by stopping the valves when not in use. Water consumption was reduced by 30% from 8,100 m3/month in the second half of 2022 to 5,700 m3/month in the full year of 2023 after the completion of measures to increase the production of mask tapes.