Basic Concept
The Nisshinbo Group's Business Conduct Guidelines include Awareness and Concern towards its environmental impact. The Group provides energy conservation technologies, products, and services, as well as its own energy conservation measures, and faithfully realizes a safe and secure society for all people. The Group manages key performance indicators (KPIs) as part of systematic measures to achieve its environmental target of reducing energy use per unit of sales.
【Main measures】
- ① Promoting activities to curb energy consumption through ISO 14001 activities
- ② Selecting environmentally friendly equipment when renewing equipment and continuously implementing energy conservation measures through improvement activities
- ③ Systematic use of LEDs for lighting
- ④ Pursuit of the introduction of energy conservation equipment in new buildings and warehouses and the reduction of energy consumed by air conditioning
Please refer to "Promotion System" in "Environmental Management" for the promotion system.
Specific Initiatives of The Nisshinbo Group
Energy Use by Type of Fuel
The Nisshinbo Group’s energy usage in FY2023 amounted to 8.62 million GJ, down 4% year-on-year (YoY). Energy usage per unit of sales was 16.23 GJ/million yen, down 6% YoY.
PT. Nikawa Textile Industry in Textiles business stopped using coal boilers to generate electricity and switched to purchasing electricity from November 2021, which resulted in a significant reduction in coal consumption and a decrease in energy consumption per net sales. In FY2023, the Group's energy use and energy use per sales decreased further from production cuts in the Textiles business and the transfer of TMD in the Automobile Brakes business.
By type of fuel used, electricity accounted for 87% of the total, and gas accounted for 8%.
Trends in the Amount of Energy Consumed and the Amount of Energy Consumed per Unit of Sales
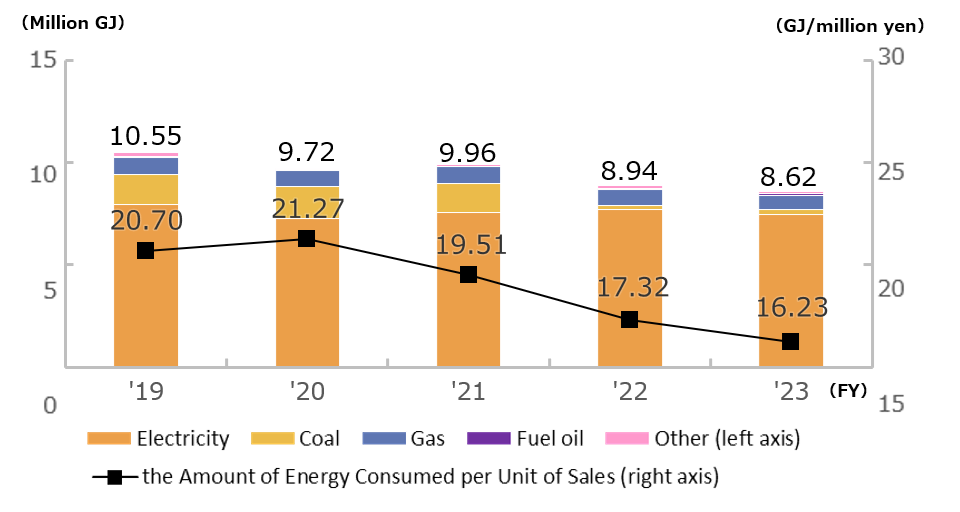
*1 Because of the transfer of all shares of TMD FRICTION GROUP S.A. (TMD), a subsidiary in the Automobile Brakes business, on November 30, 2023, and for other factors, TMD and 21 other companies were excluded from the scope of consolidation. Therefore, TMD and 21 other companies are included in the data until November 2023.
*2 On December 27, 2023, HVJ Holdings, Inc. and its subsidiary Hitachi Kokusai Electric Inc. and 7 other companies were included in the scope of consolidation, but are not included in the data for FY2023.
Amount of Energy Consumed by Business
The Automobile Brakes business accounts for the largest portion of energy consumed, at 2.88 million GJ down 3% YoY, followed by the Micro Devices business at 2.09 million GJ down 2% YoY.
Amount of Energy Consumed by Business
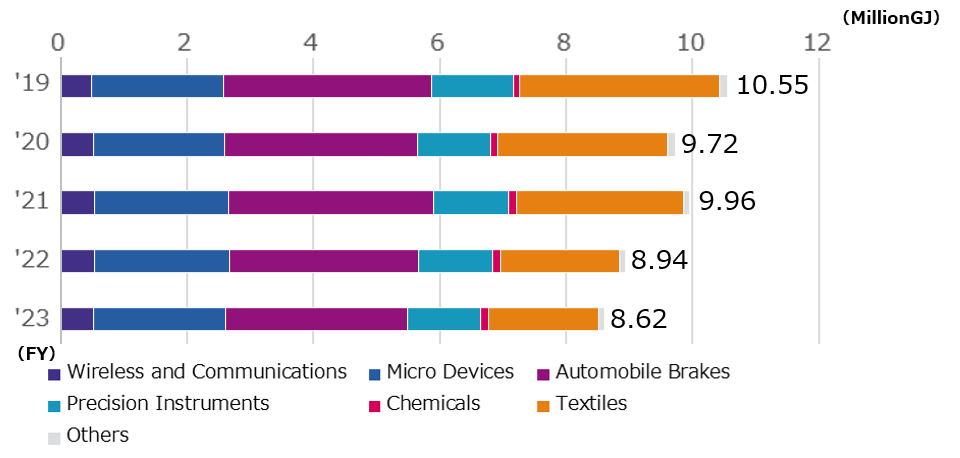
*1 Because of the transfer of all shares of TMD FRICTION GROUP S.A. (TMD), a subsidiary in the Automobile Brakes business, on November 30, 2023, and for other factors, TMD and 21 other companies were excluded from the scope of consolidation. Therefore, TMD and 21 other companies are included in the data until November 2023.
*2 On December 27, 2023, HVJ Holdings, Inc. and its subsidiary Hitachi Kokusai Electric Inc. and 7 other companies were included in the scope of consolidation, but are not included in the data for FY2023.
Effect of Introducing LED Lighting
The energy conservation impact of new conversion to LED lighting in FY2023 was 1081 MWh, as indicated in the table below.
The use of LEDs is being systematically promoted at Japan Radio Co., Ltd. Ueda Logistics Center and Mitaka Office in the Wireless and Communications business; Nisshinbo Micro Device Inc., Kawagoe Plant in the Micro Devices business; and Nisshinbo Mechatronics Inc., Miai Machinery Plant in the Precision Instruments business.
Reduction in Electricity Consumption
Business Category | Reduced Consumption(MWh) |
---|---|
Wireless and Communications | 421 |
Micro Devices | 268 |
Automobile Brakes | 143 |
Precision Instruments | 200 |
Chemicals | 7 |
Textiles | 6 |
Real Estate | 36 |
Total | 1,081 |
*1 Because of the transfer of all shares of TMD FRICTION GROUP S.A. (TMD), a subsidiary in the Automobile Brakes business, on November 30, 2023, and for other factors, TMD and 21 other companies were excluded from the scope of consolidation. Therefore, TMD and 21 other companies are included in the data until November 2023.
*2 On December 27, 2023, HVJ Holdings, Inc. and its subsidiary Hitachi Kokusai Electric Inc. and 7 other companies were included in the scope of consolidation, but are not included in the data for FY2023.
Specific Activities of the Group Companies
Promote energy conservation Activities by Switching to LED Lighting Equipment
Each company in the Wireless and Communications Group is promoting energy conservation activities by switching to LED lighting equipment.
Japan Radio Co., Ltd. has been working on a five-year plan to convert the lighting equipment at its Ueda Logistics Center to LEDs. In the third year of the five-year plan, the lighting equipment on the first floor of the north building and the first floor of the south building was converted to LEDs, and some lighting equipment at the Mitaka Office and the Shizuoka Sales Office were also converted to LEDs. In FY2023, the company expects to reduce electricity consumption by 299 MWh by converting to LED lighting at two offices and one sales office.
In FY2023, Nagano Japan Radio Co., Ltd. implemented LED conversion of fluorescent lights (379 lamps replaced) at its Head Office & Factory, achieving an LED conversion rate of 77%. Nagano Japan Radio will continue to promote the use of LEDs for fluorescent lighting on the premises from next year onward and plan to increase the LED conversion rate at the Head Office & Factory to more than 80% by FY2024.
Ueda Japan Radio Co., Ltd. has been promoting the use of LED lighting equipment under a five-year plan starting in FY2023. A total of 280 lighting fixtures on production lines at the Komaki Plant were replaced with LED lighting in FY2023.
Energy Conservations Through the Introduction of Next-Generation Environmentally Friendly Refrigeration Equipment
Nisshinbo Micro Devices Fukuoka Co., Ltd. has selected and introduced a next-generation environmentally friendly non-CFC inverter-turbo refrigerator*1 as an energy conservation measure for its power equipment.
The company's turbo chillers consisted of a 6,600 V supply power system with a refrigeration capacity of 500 RT (three units), and considering that the load varied because of seasonal fluctuations, the following two operations were used:
- ① Two units in commercial operation in spring to fall (three units in operation under heavy load)
- ② In winter, cooling tower free cooling*2 one unit + one commercial unit operation or two units commercial operation
From March 2023, the installed chillers were put into operation with one inverter machine and one commercial machine in operation from spring to fall, resulting in a reduction of 968 MWh/year (418 t-CO2/year of CO2 emissions) in electricity consumption for the chillers compared to the previous year.
*1 Turbo chillers manufactured by Mitsubishi Heavy Industries Air-Conditioning & Refrigeration Corporation, which are exempted from the High Pressure Gas Safety Act and use environmentally friendly non-CFC refrigerants (1233zd(E), GWP:1).
*2 A method of producing chilled water by operating the cooling tower and pumps without moving the chiller, utilizing natural cooling by the outside air.
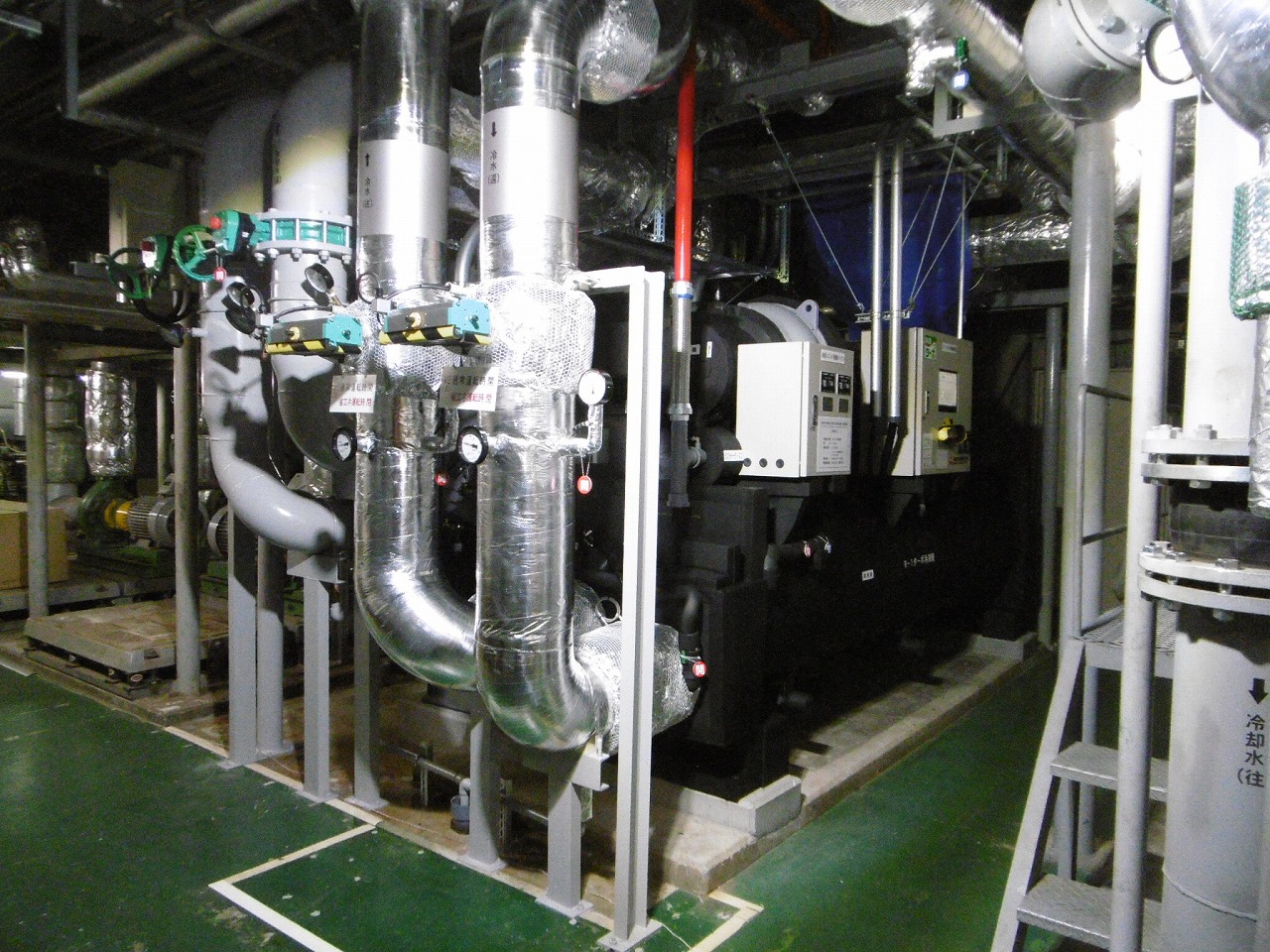
Effectiveness of Energy Conservation Measures
Nisshinbo Micro Devices Fukuoka Co., Ltd. implemented the following energy conservation measures for ① power and ② production facilities with the goal of reducing electricity consumption by 1% or more compared to the previous year and by 13% (4,612 MWh/year) or more compared to FY2014 by the end of FY2023.
- ① Reduction of 2,637 MWh/year (CO2 emissions: 1,166 t-CO2/year) from the previous year, including the introduction of next-generation environmentally friendly non-CFC inverter-turbo refrigerator units and renewal of dry-air primary dryers.*
- ② Power saving and halting to reduce wasteful power consumption by identifying production facilities that do not contribute to production, resulting in a reduction of 193 MWh/year (CO2 emissions: 92 t-CO2/year) compared to the previous year.
As a result of these effects, the company achieved the target with a reduction of 2,830 MWh/year (CO2 emissions: 1,259 t-CO2/year), down 9% from the previous year, and 6,962 MWh/year (CO2 emissions: 8,721 t-CO2/year), down approximately 20% from the FY2014 level.
Nisshinbo Micro Devices Fukuoka will continue to introduce high-efficiency equipment for power equipment (pumps/motors), promote the use of inverters for water pumps and exhaust fans, and continue the environmental load reduction (energy conservation and prevention of global warming) activities, including consideration of renewable energy and solar power generation.
* Equipment that cools compressed air produced by a compressor through a heat exchanger using refrigerant gas to remove moisture.
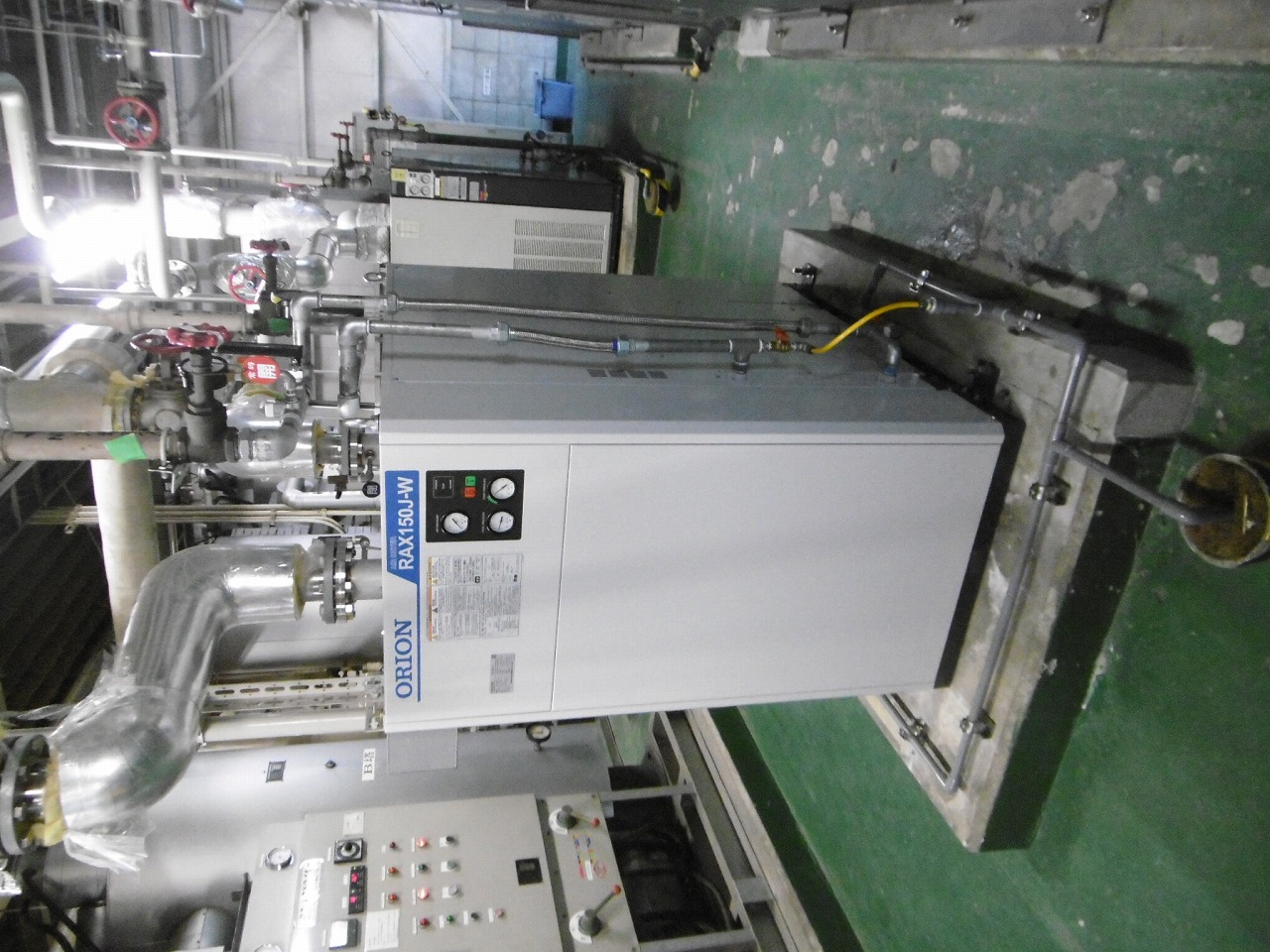
Energy Conservation Activities Through the Use of LED Lighting Fixtures
Nisshinbo Micro Devices AT Co., Ltd. is converting its lighting equipment to LED as needed.
In 2023, the project focused on a portion of the plant production floor and attached buildings and rooms and included approximately 30 locations for unplanned failure repairs. Some locations related to production areas (Kitchen for lunch room, cafeteria area, parts warehouse, packaging room, stairs, etc.) are lit throughout the day (24 hours), resulting in a significant effect. Overall, the LED conversion has reduced power consumption by a total of 35 MWh/year (CO2 reduction: 17 t-CO2/year).
The company plans to promote the conversion of lighting fixtures to LEDs as a priority energy conservation measure in the next fiscal year and beyond. In addition to lighting fixtures, the company has also implemented heat insulation improvements to steam pipes inside and outside the boiler room (to prevent losses due to thermal energy release) and replaced air compressor equipment with high-efficiency machines (to reduce electricity consumption), resulting in an overall reduction of 45 t₋CO2/year in CO2 emissions.
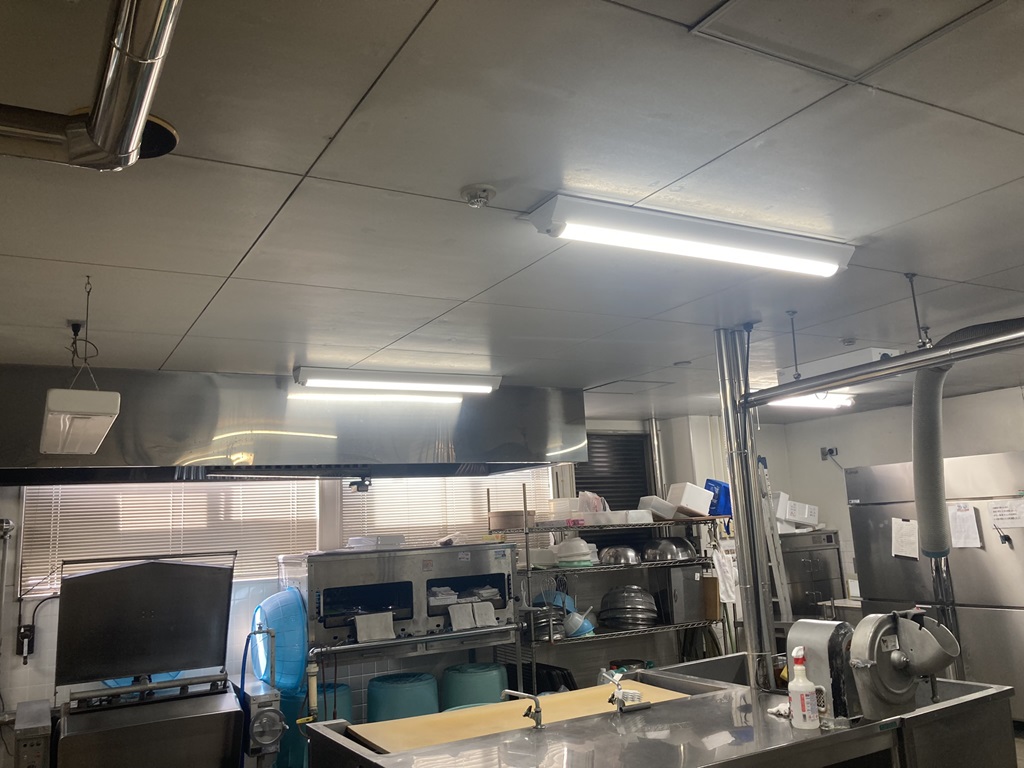
Raise Awareness of Energy Conservation by Publishing Energy Conservation Newspapers
Nisshinbo Mechatronics Inc. Miai Machinery Plant publishes an energy conservation newspaper once a quarter as a measure to raise awareness of energy conservation activities by all employees working together to promote them, taking a step forward from the energy conservation activities conducted by the committee to date.
This newspaper is designed to provide concise information on the activities of the Energy Conservation Activities Committee and topics related to energy conservation with a focus on what energy conservation activities are being conducted now, why energy conservation activities should be promoted, and how they can lead to energy conservation. The report was created with an eye to making it easy for all employees to feel that energy conservation activities are their business.
The publication of this energy conservation newspaper and the promotion of activities through the Energy Conservation Activity Committee and Kaizen in the workplace have had the effect of leading to more active energy conservation activities than ever before, leading to the proposal of 34 Kaizen projects in FY2023 (29 of which have been implemented) for the year, and the result value of energy conservation at the end of FY2023 far exceeded the target value.
Target: 45 MWh/year (excluding capital investment)
Result: 88 MWh/year (CO2 reduction: 40 t-CO2/year)
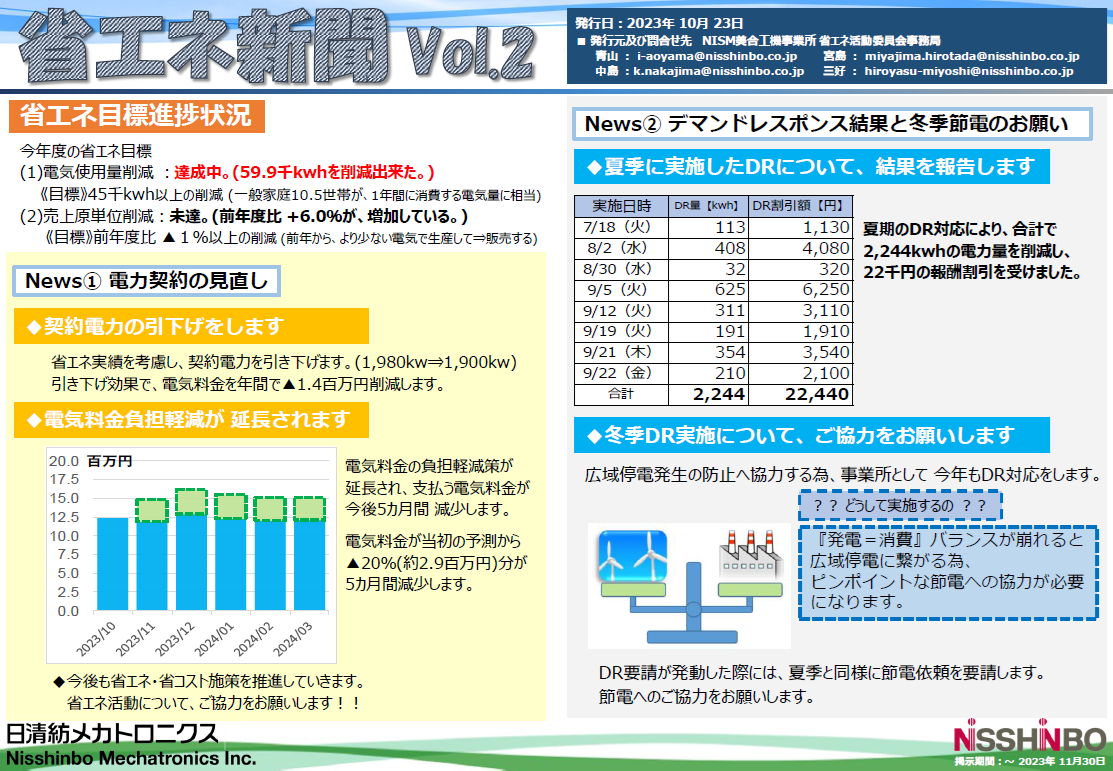
Reduction of Electricity Consumption by Changing the Temperature Control System
Nisshinbo Chemical Inc. Tokushima Plant manufactures the resin additive CARBODILITETM in a reaction vessel. During the manufacturing and cleaning processes, high-temperature and low-temperature heat-transfer oils are constantly circulated and supplied to the necessary reaction vessel when necessary.
The company investigated the optimal circulation flow rate for the current monthly production schedule for the heat transfer oil circulation rate set at a high temperature. As a result, the company found that it is possible to reduce the circulation flow rate, and through valve adjustment, Nisshinbo Chemical reduced the actual result by 11.5 MWh in FY2022.
One of the heat transfer oil circulation pumps set at a low temperature is dedicated to one reaction vessel. The system program had been designed to operate continuously from the temperature control process to the end of the batch manufacturing process, but the company has subdivided the process into smaller processes in the system program and changed the program to operate the pumps during the temperature control process and stop the processes that do not require temperature control. As a result, the company reduced 10.8 MWh in FY2022 actuals.
Energy Conservation Measures at Production Sites
Nisshinbo Textile Inc. Tokushima Plant has five factories, the oldest of which is a chemical plant factory that has been in operation since 1983. In 2023, the following energy conservation measures were implemented
- ① Drive motors for raw material feed pumps, raw material mixing equipment, and blowers for the constant temperature chamber were changed from standard efficiency motors to high efficiency motors. Or, general-purpose motors were changed to the inverter type.
- ② The lighting in the hall was changed to the LED type, and motion sensors were installed for some of them.
- ③ The entire air-conditioning system was replaced with spot air-conditioning with resin curtains separating only the necessary work areas.
- ④ The spot cooler used for work has been changed to an on/off operation each time.
These measures reduced electricity consumption by 78 MWh/year and greenhouse gas emissions by 42 t-CO2/year.
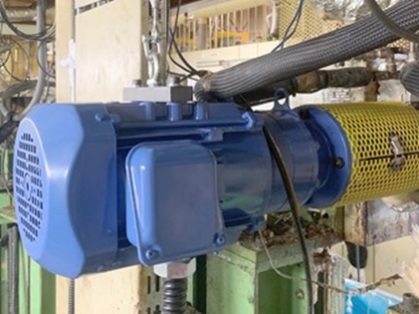
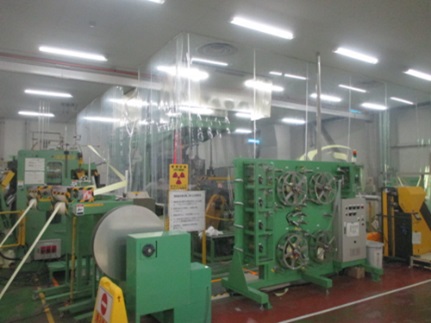
Energy Conservation Measures by Steam Drain Recovery
PT. Nisshinbo Indonesia has been progressively adding drain recovery equipment, and in 2023, 13,800 m3 of drain was recovered and reused in boiler feed water. This means that 57.7 GJ of energy to raise boiler water temperature and 13,800 m3 of water was saved.
Textile processing includes removing the sizing agent used in weaving the fabric, whitening the fabric by removing impurities from the fibers, and dyeing the fabric, but most of the processes involve wetting and treating the fabric. At each stage of the process, dough is dried using a cylinder dryer that utilizes steam. The cylinder dryer has a metallic cylindrical structure. Water vapor generated by a boiler is placed inside the metallic cylinder to dry the dough by bringing it into contact with the cylinder's surface. The steam used in this process cools down to form water droplets (drain), which has high thermal energy and is pure water with no impurities.
* Drain recovery: Recovering drain that has sufficient sensible heat discharged from the steam trap and reusing it in some form, rather than just throwing it away.
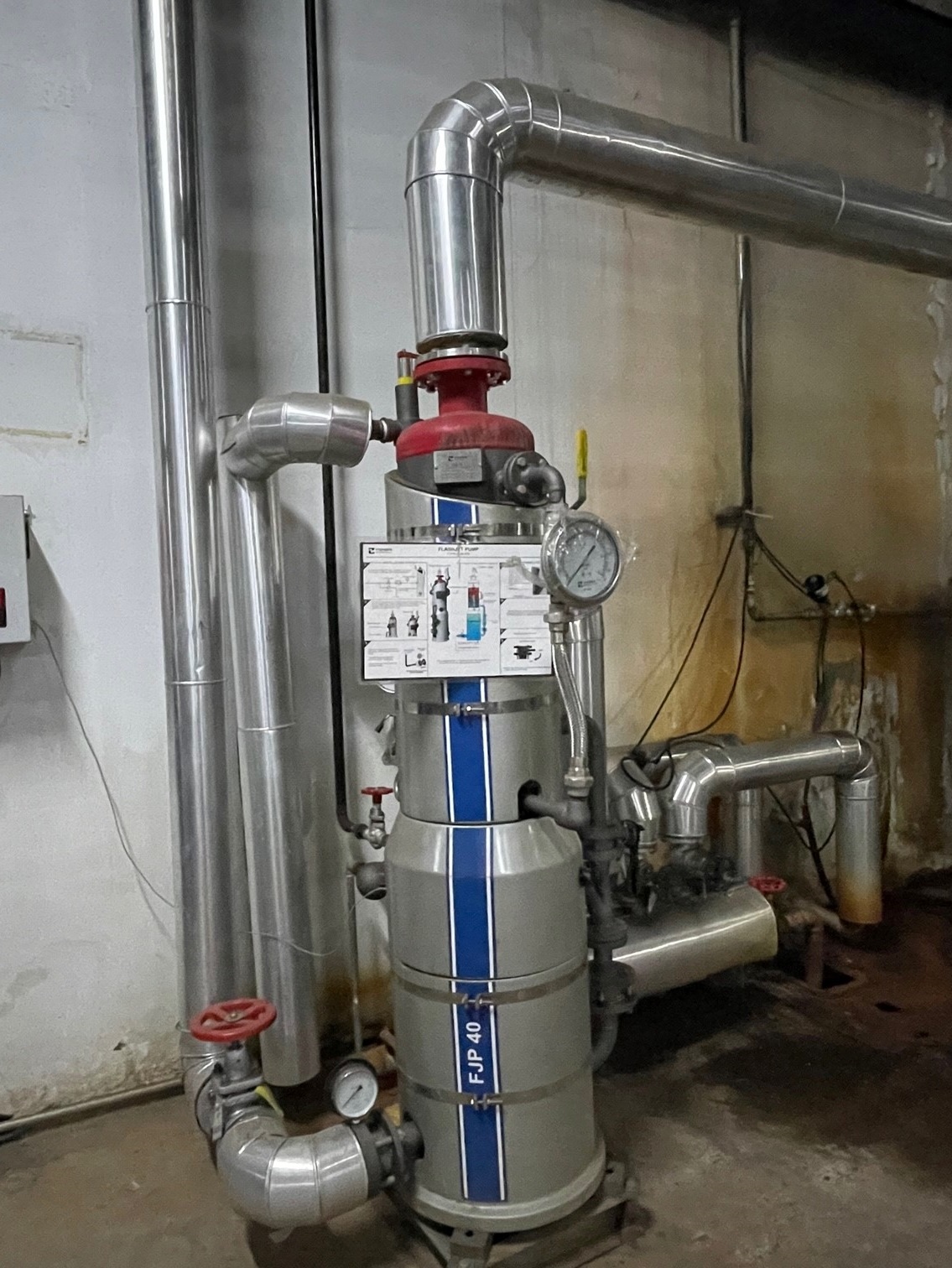
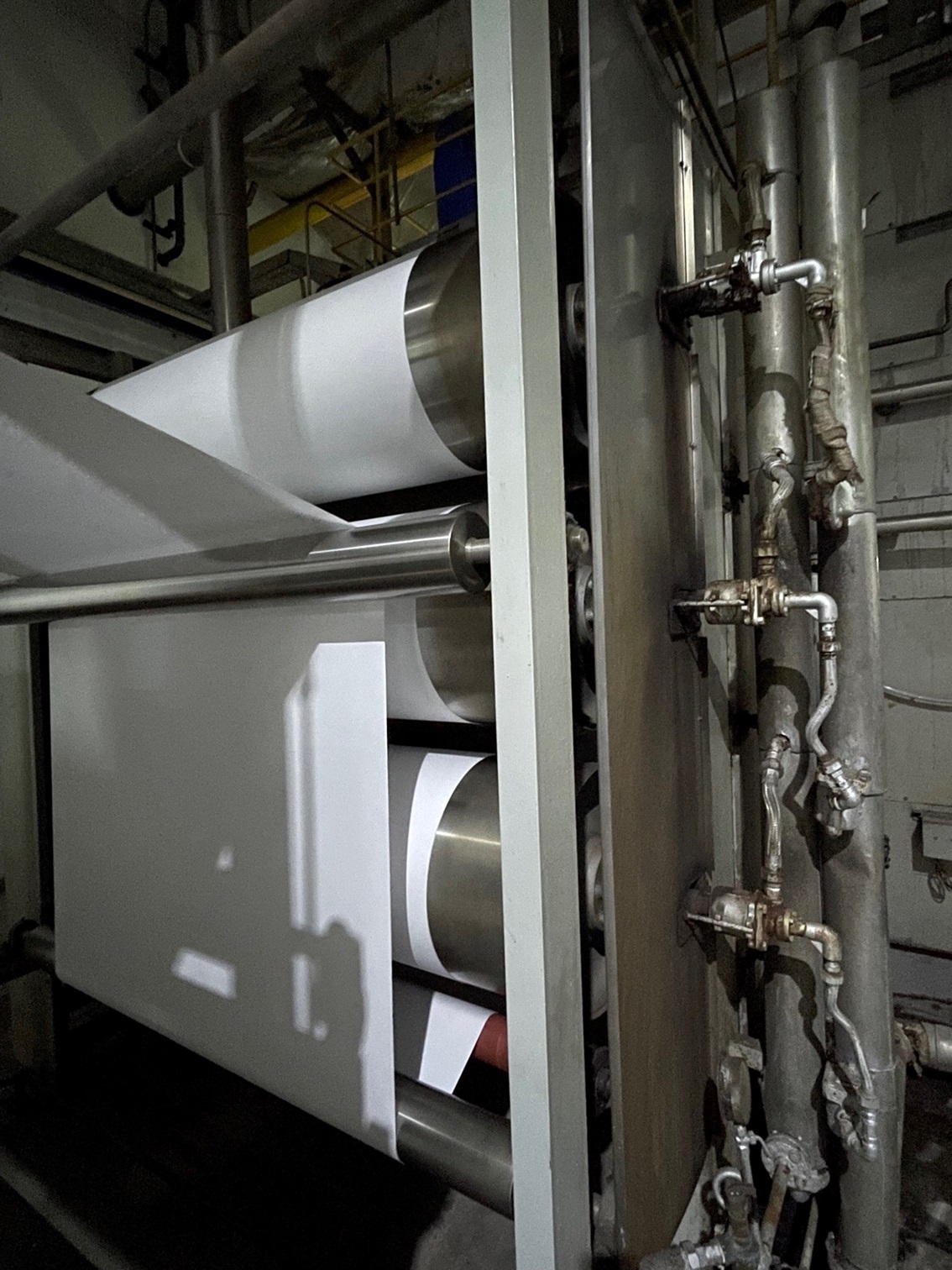