Basic Concept
The Nisshinbo Group's Business Conduct Guidelines states that "Safety is the Basis for Everything" and clearly states that the Group holds safety as the top priority for all of its activities to bring high-quality products to customers.
Promotion System
The Nisshinbo Group has established a Group Health and Safety Liaison Conference to promote the prevention of occupational accidents throughout the Group. Under a system in which the director and the chief of the Corporate Strategy Center of Nisshinbo Holdings Inc. serves as group supervisor, The Health & Safety Group of the Sustainability Development Department of the Corporate Strategy Center serves as the secretariat and is working on the activities. To promote activities for occupational safety and health based on the Sustainability Promotion Plan, targets and Key performance indicators (KPIs) are managed, and measures are implemented.
In addition, a management review is conducted at Board of Management of Nisshinbo Holdings Inc. on the Group's progress in achieving targets, the status of occupational accidents, and the results of health and safety audits, and the president and the director, who is the chief executive officer, provides instructions on targets and priority policies for the following year. Management reviews are also reported to the Board of Directors.
Specific Initiatives of the Nisshinbo Group
In the "Fifth Sustainability Promotion Plan," the Group designated the promotion activities for occupational safety and health as a key action items and is working to prevent occupational accidents. The Nisshinbo Group is working to achieve the goal by implementing the PDCA cycle and the number of serious accidents "0" as a KPI.
In FY2024, the Nisshinbo Group will continue its efforts to prevent serious accidents, strengthen chemical substance management, and promote preventive measures for behavioral accidents under the priority policy of strengthening safety and health activities as was done in FY2023.
The main specific activities in FY2023 were as follows;
-
- ① Prevention of serious accidents
- When introducing new machinery, equipment, or new chemical substances, or when making major changes in work content, risk assessment is utilized to promote measures to reduce major risks.
-
- ② Strengthen preventive safety activities
- Re-establish a system for autonomous chemical substance management at each business location.
-
- ③ Improvement of hazard sensitivity
- Improve each employee's sensitivity to danger by improving communication through hazard prediction training and Hiyari-Hatto (near-miss) reporting activities.
Occurrence of Occupational Injuries
In FY2023, the Nisshinbo Group had no serious occupational accidents (classified as grade 1 to7 death or disabilities).
The frequency rate of lost time injuries,* which represents the frequency of occupational accidents, worsened compared to FY2022 for the Japan group as a whole, but remained at a favorable level compared to the Japanese manufacturing industry.
When an occupational accident occurs, the person in charge of health and safety and the manager or supervisor of the department where the accident occurred conduct interviews the workers involved, including those affected, to determine the true cause and to implement measures to prevent a recurrence. In addition, the details of the occupational accident and countermeasures are compiled into a report and disseminated to all Nisshinbo Group companies to help prevent similar accidents.
* Frequency of injuries with lost work days: an index of the frequency of injuries with lost work days. Expressed as the number of work-related fatalities and injuries per 1 million total working hours.
Frequency of Injuries with Lost Work Days
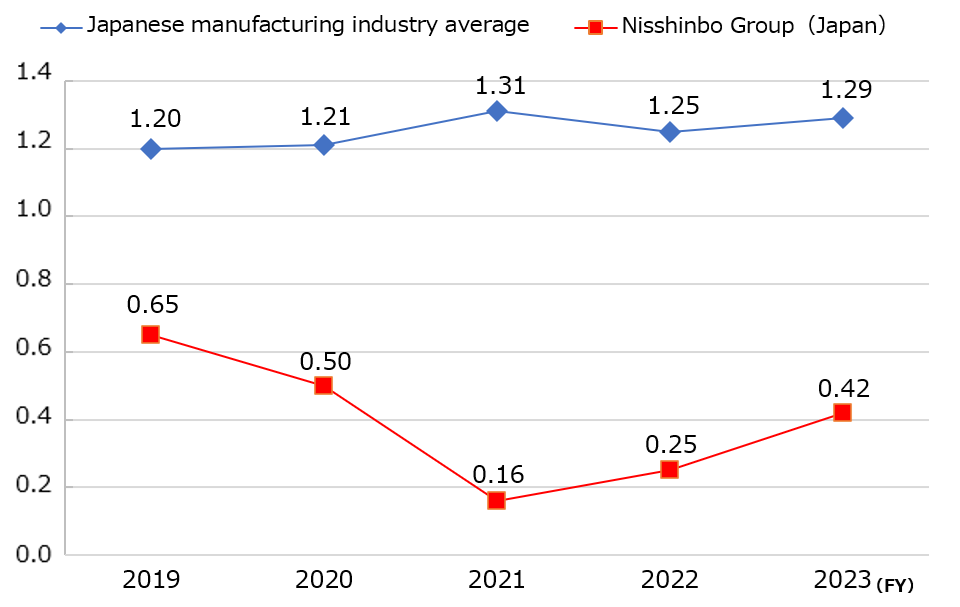
Safety and Health Activities and 5S Activities
In addition to education at the time of hiring and at the time of changes in work content, each business site of the Nisshinbo Group strives to raise the safety awareness of each and every employee through small group activities and training to improve the abilities of employees engaged in safety and health work, hazard prediction training, 5S (Sorting, Setting-in-Order, Shining, Standardizing, Sustaining the Discipline) activities, and risk simulation education. Nisshinbo also formulates annual plans and systematically conducts risk assessments of equipment, operations, and chemical substances to determine priorities and implement preventive safety measures.
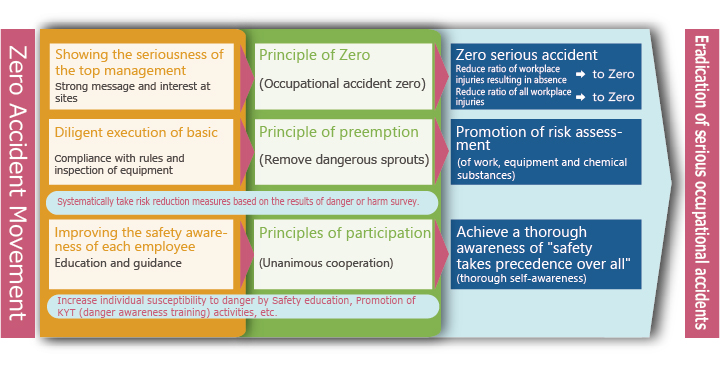
Health and Safety Education and Training
In accordance with the Nisshinbo Group's priority policy for FY2023 of strengthening safety and health activities, the event provided an opportunity to learn about the implementation status of safety and health management and safety and health activities at the complex business sites. A total of 77 persons in charge of safety and health at each business site participated.
The Nagano Plant, the site of this study session, comprises five companies: Japan Radio Co., Ltd., Nagano Japan Radio Co., Ltd., Nagano Japan Radio Manufacturing Co., Ltd., JRC logistics Co., Ltd., and JRC Mobility Inc. The participants exchanged opinions on jointly conducted safety and health activities and issues related to the commonization of rules.
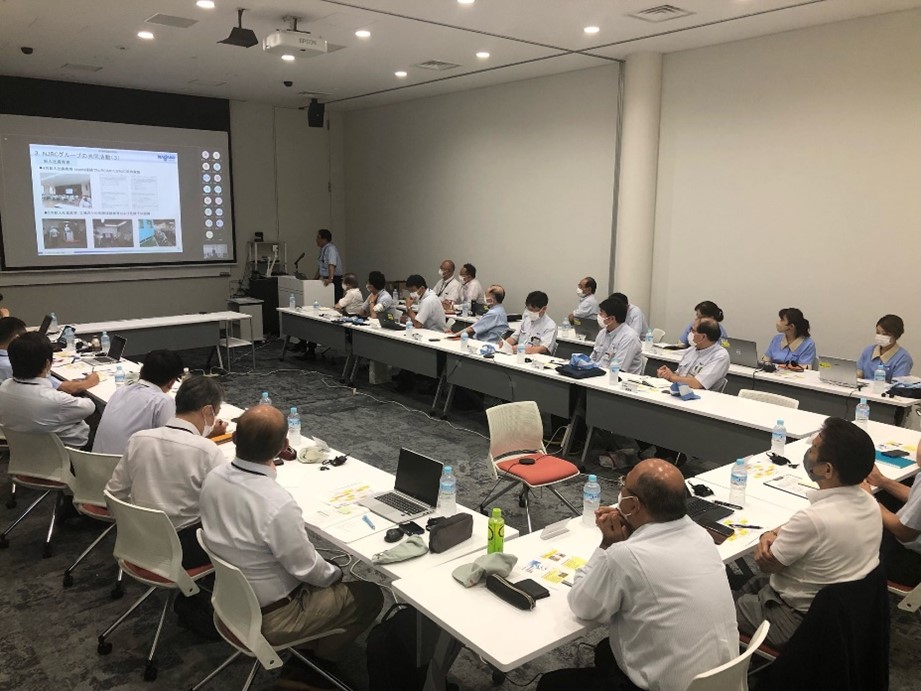
Safety and Health Audits
The Nisshinbo Group periodically audits the status of health and safety management at each business site by organizing an audit team consisting of the Health & Safety Group of Nisshinbo Holdings Inc., the labor union, health and safety managers representing operating companies, and health and safety managers from other business sites. In FY2023, Nisshinbo conducted health and safety audits at 46 business sites in Japan, mainly manufacturing sites, and 4 overseas business sites.
At the end of the fiscal year, the monitoring team prepare a comprehensive audit report based on these audit results. The team also share accident risk analysis results and case studies of excellent activities throughout the Group and incorporate them into occupational safety and health activities in the following fiscal year.
Chemical Substance Management Initiatives
From 2023, autonomous management of chemical substances has been required because of the revision of government ordinances related to the Industrial Safety and Health Act. Since chemical substances are used at many business sites, a study group was held with experts from domestic group companies to develop Guidelines for Chemical Substance Management at Workplaces and deployed them to all business sites so that they can respond to autonomous management without omissions. The study group will continue in 2024 to exchange information with the departments in charge on the status and challenges of management in accordance with the guidelines.
Activities at Business Sites in Overseas
Overseas group companies strive to raise the awareness of safety by each employee through the implementation of danger-detection training and danger-perception training provided at each site in cooperation with the core companies under its jurisdiction in accordance with the Guidelines for Behavior with the "Safety is the Basis for Everything." In addition, the Nisshinbo Group works to prevent the recurrence of occupational injuries at sites within the Group companies and to prevent similar injuries. Regarding the chemical substances handled, the Group continue to disseminate the danger and thoroughly implement the use of protective equipment to prevent health problems.
Specific Activities of the Group Companies
One Word KY Presentation to Increase Sensitivity to Danger
At JRC Tokki Co., Ltd. a one-word presentation on hazard prediction (KY) is given at each department's morning meeting as an activity to increase sensitivity to danger.
Each presenter gives a presentation on the hazards the employee perceives while commuting or working, and a list of these hazards is compiled and disseminated throughout the company, along with comments from department managers.
Many accidents and disasters are caused by human error. In order to eliminate these human error accidents, it is necessary to implement physical measures, such as machinery and equipment, and management measures, such as knowledge and skills training related to safety and health. Hazard prediction (KY) activities are conducted to help each individual sharpen his or her sensitivity to danger and improve concentration at key points of action.
The one-word presentations were developed for commuting, such as slips and falls during rain and snowfall and bicycles driving on the left side of the road, and for work, such as preventing falls when moving loads on a cart. In FY2023, there were 740 cases announce.
Disaster Prevention, Safety, and Health Activities
Nisshinbo Micro Devices Fukuoka Co., Ltd. has set a goal of zero disasters and conducts disaster prevention safety and health activities with a spirit of self-reliance and altruism.
-
① Workplace improvements that take into account older workers
A step standardization team was formed and all steps existing in the company were measured; steps were defined as 5.0 mm or more in reference to the JIS standards, and regulations were established and put into operation to standardize the method of displaying warning signs. In addition, clean shoes designed to prevent tripping were introduced and distributed to older workers in turn. -
② Measures to prevent accidents during commuting by bicycle
A Safety Protection Team of selected bicycle commuters was formed to strengthen the follow-up system by providing assistance in inspecting bicycles for commuting and consultation on repairs. Education for bicycle commuters is provided once a year, and voluntary bicycle inspections are conducted twice a year. -
③ Measures to prevent work-related accidents due to the transportation of heavy objects
Specialized carts and storage racks were built in-house to avoid transporting heavy items by hand. In addition, regulations to standardize the handling of heavy materials were established and put into operation.
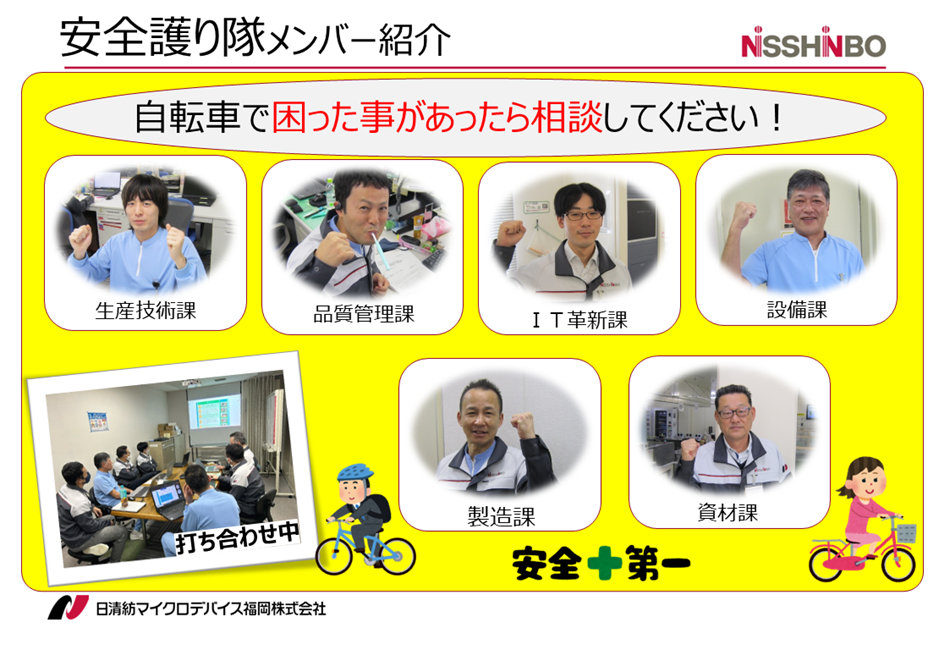
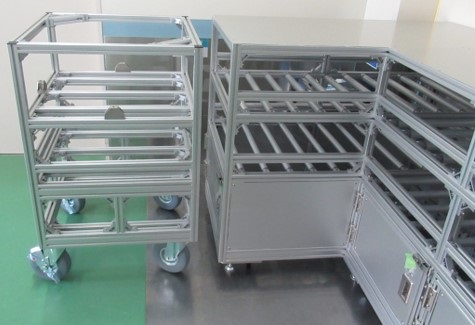
Promote Acquisition of Safety Basic Assessor certification
Nisshinbo Micro Devices AT Co., Ltd. has been working to acquire the Safety Basic Assessor* qualification since 2021, mainly for maintenance workers in the manufacturing department, as an activity to reduce the risk of accidents in the workplace. Through this certification, it is expected to increase safety awareness, foster a sense of security, and improve wellbeing, thereby raising the level of safety awareness throughout the manufacturing site.
In 2023, 20 new members obtained the certification, bringing the total number of certified members to 32 out of 85, for a certification rate of 38%. The company will continue to ensure safe operations by having all maintainers obtain the certification.
* It is a safety certification that certifies universal and basic knowledge of machine safety as defined by the Japan Certification Corporation and is also specified in the Ministry of Health, Labor and Welfare's notice as effective for machine safety education for machine users' foremen, work supervisors, and safety personnel.
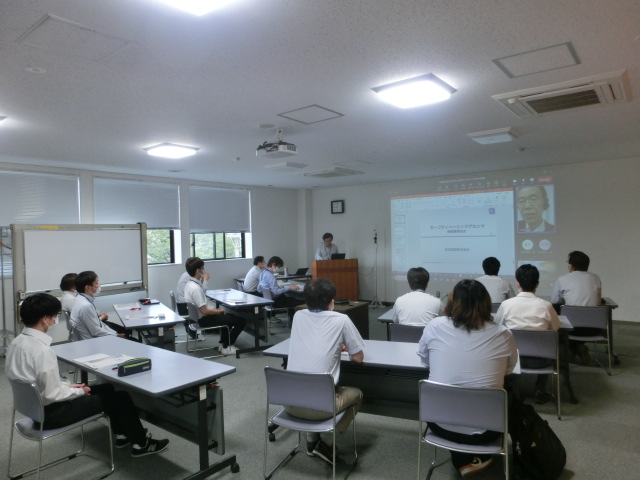
Received the National Award for Excellence in Safety and Health
Nisshinbo Micro Devices (Thailand) Co., Ltd. received the first Safety and Health Excellent Workplace Award from Lamphun Province in 2004 with the aim of providing a safe work environment within the company and raising employee safety awareness through safety and health activities. Since then, the company has received the Lampoon Province Safety and Health Excellence Award for five consecutive years, and in 2009, the sixth year of the award, the company received the National Level Safety and Health Excellence Award for the first time.
In FY2023, the company participated in the Safety and Health Excellent Workplace Contest organized by the Department of Labor Protection and Welfare, Ministry of Labor, Thailand. As a result, the company was awarded the Platinum Level of the National Safety and Health Excellent Workplace Award for the 20th consecutive year for the various safety, health, and welfare promotion activities implemented in FY2022. The company was represented by Mr. Nongnut, Administrative Director, and Mr. Chalinrat, Chief of the Safety and Health Promotion Division, who attended the award ceremony held at the Ministry of Labor in Bangkok on September 18, 2023.
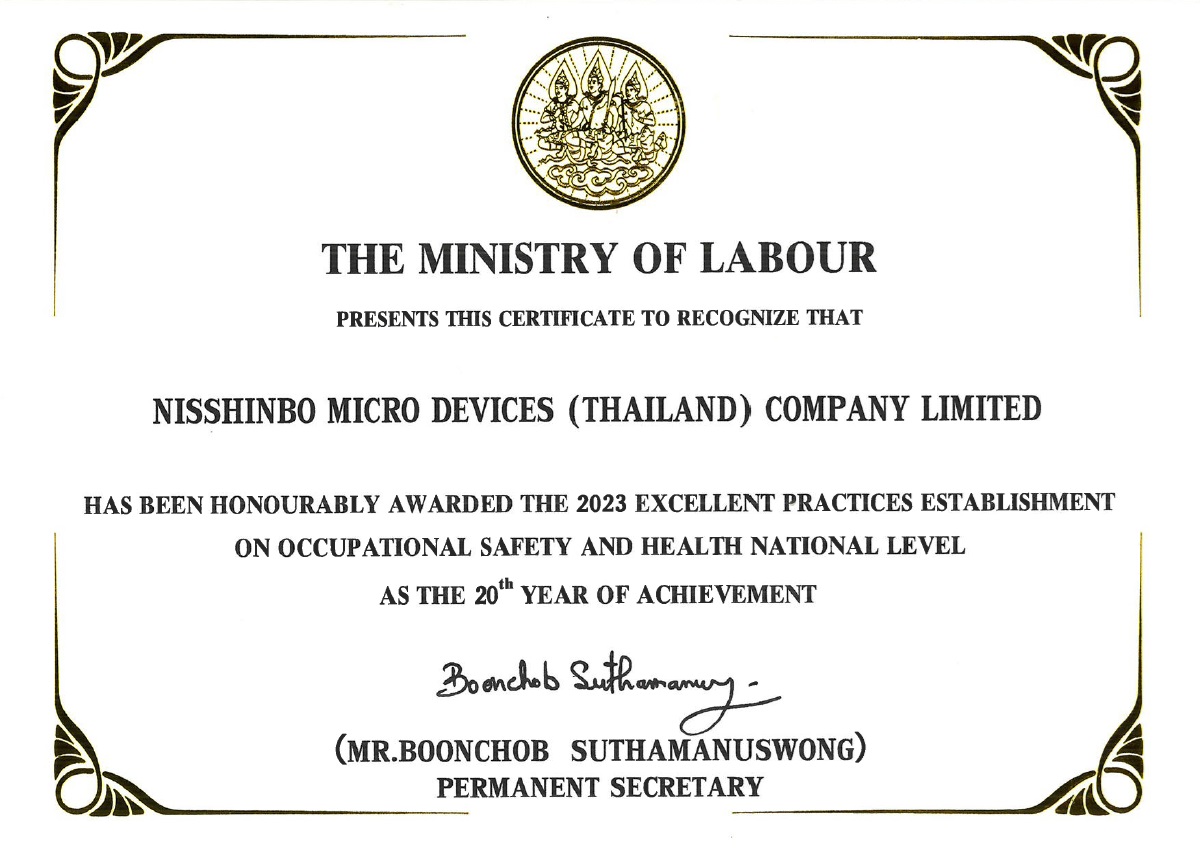
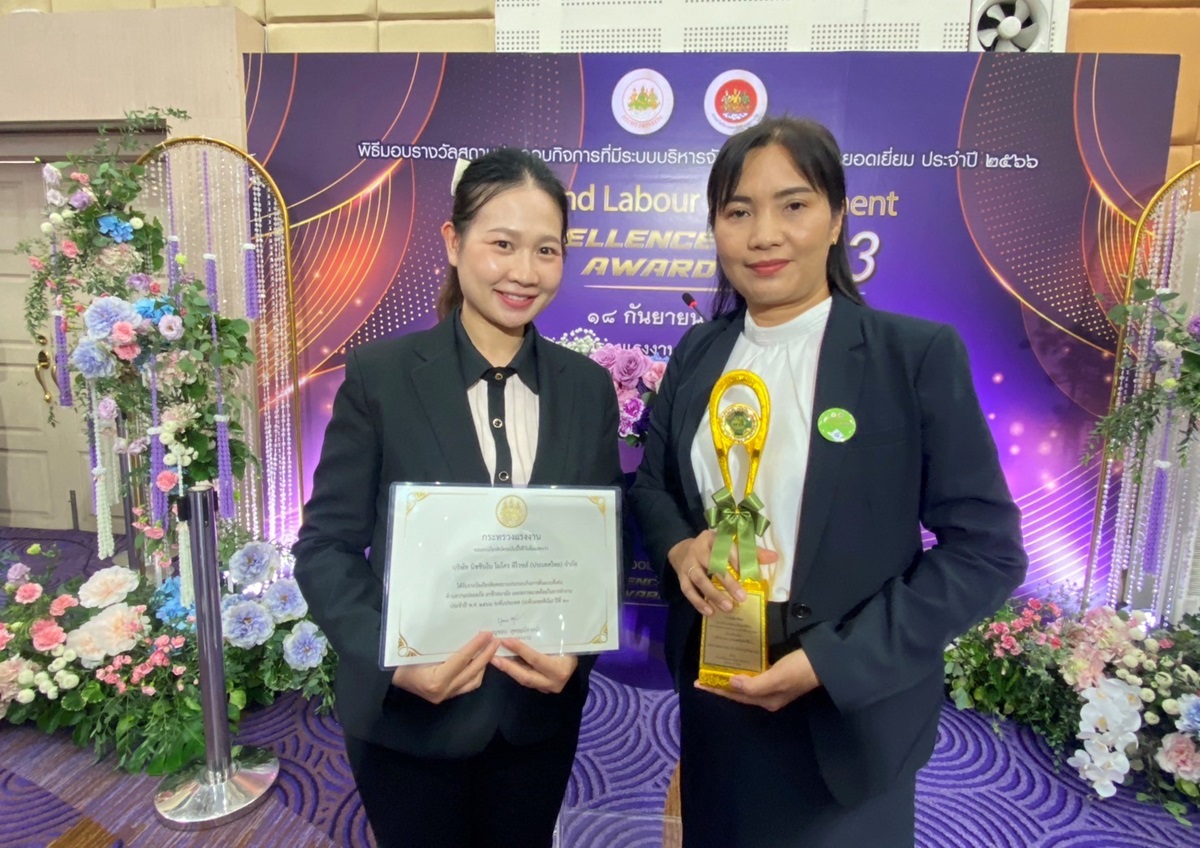
Efforts to Enhance Safety and Health Education
The Nisshinbo Brake Inc. Tatebayashi Plant is working to enhance safety and health education. Among these, training for foremen has traditionally required completion of an external training course conducted by a designated corporation in accordance with the Safety and Health Law.
In order to achieve flexible and effective in-house training that is consistent with in-house safety and health training at the worksite and in line with work content, safety and health staff obtained the Ministry of Labor Method Safety and Health Training Trainer for Worksite Supervisors (RST) certification, which is an instructor requirement for implementing training for worksite managers. The company has a proven track record of providing timely foreman training by following the designated curriculum for foreman training, creating educational content tailored to the work content of the business site, and scheduling it flexibly to coincide with the timing of the appointment of foreman. In addition, in-house simulated occupational injury training is also regularly conducted by instructors with RSTs, in coordination with each safety and health training program.
The company is working to enhance in-house safety and health education while improving the skills of its safety and health instructors. The company hopes that these daily efforts will lead to the maintenance and improvement of safety and health awareness in each workplace.
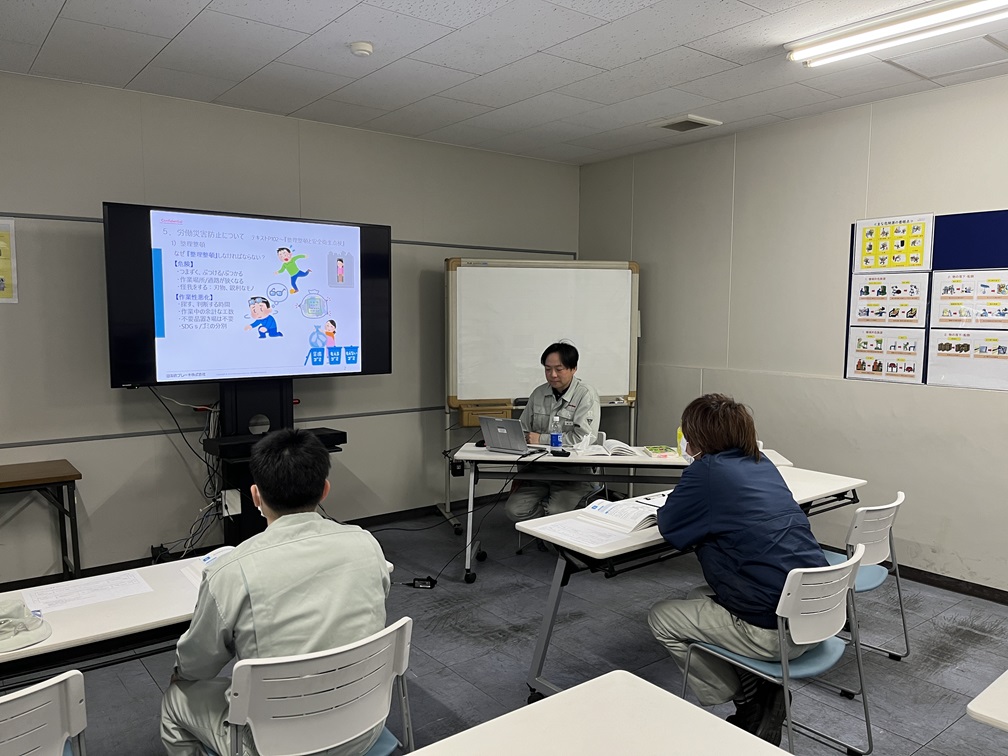
Promote Safety Activities
At Nisshinbo Automotive Manufacturing Inc. (NAMI) in the United States, all accidents and incidents are thoroughly investigated by the safety team and management to determine the cause and implement corrective actions to prevent similar incidents.
<Main Safety Activities>
- ① Sharing daily safety messages
- ② Creation and posting of alert materials to prevent the recurrence of accidents and similar incidents
- ③ Post monthly safety topics
- ④ Start of "PPE audit walks (checking personal protective equipment on site)" to ensure NAMI's safety management policy
Holding of The 5S Contest
In FY2022, Nisshinbo Mechatronics Inc. saw further promotion of 5S (Sorting, Setting-in-Order, Shining, Standardizing, Sustaining the Discipline) activities at each of its sites through the 5S Contest Excellent Business Site Tour.
Selected teams from each site (nine domestic and six overseas) conducted the first round of judging in November. As a result, four domestic and three overseas teams participated in the final screening held on January 16 at Miai Machinery Plant. The teams that participated in the final judging were the ones that had devised activities based on the keywords "participation by all," and among them, the teams with the highest level of in-depth investigation. The team leaders made the following comments: "We will continue our efforts for further improvement."
In FY2024, the company plans to hold a Global Contest for Safety + 5S. The company will continue to promote activities that lead to improvements in safety, 5S, and quality from a variety of different perspectives.
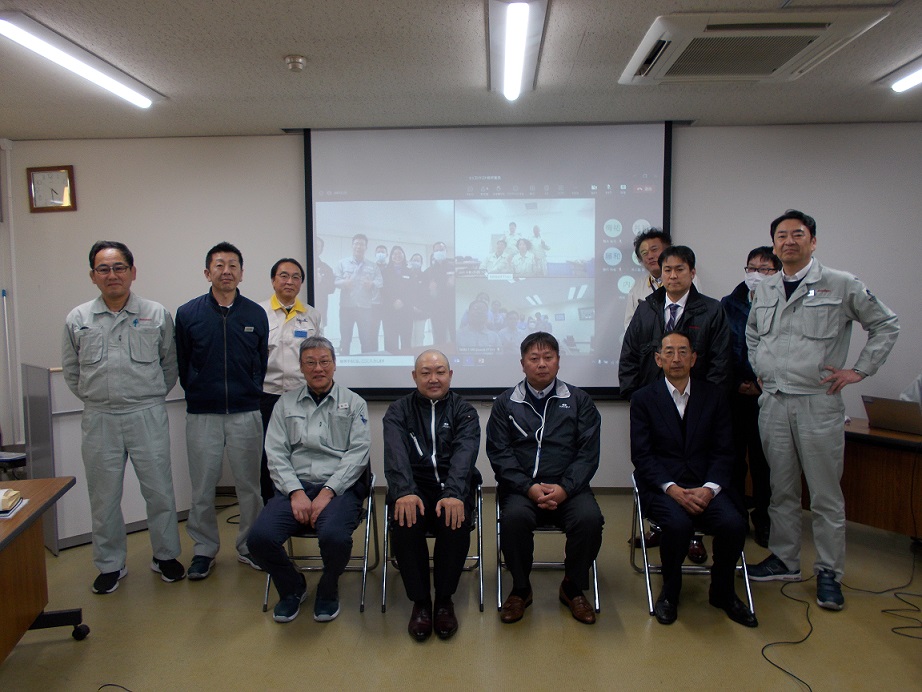
Promote Voluntary Safety Activities
Nisshinbo Mechatronics (Shanghai) Co., Ltd. conducts safety patrols (once a month) by top management and provides opportunities to receive reports on voluntary 5S and other examples of safety and health activities at each workplace.
The company has created a system that allows anyone to easily report any hazardous areas found in the company via smartphone, so that hazardous areas can be remedied quickly. The program has been in place since February 2023 with a total of 159 reports per year.
Motivation Activation
PT. Standard Indonesia Industry holds a general meeting every month to commend outstanding 5S activity teams and outstanding improvement proposals in front of all employees.
Weekly 5S patrols are conducted and each area is evaluated based on a 5S evaluation chart, including tidiness, and an outstanding team is selected based on the evaluation. As for the improvement proposals, those with the highest contribution will be selected from among the submitted proposals. At the awards ceremony, the difficulties encountered in 5S and the motivation for improvement proposals were explained in front of everyone. The company believes that this will not only motivate the employees who receive the awards but also motivate the employees who participated in the awards ceremony to aim for the awards in the next and subsequent years. The award ceremony was also posted on the company's SNS and received a lot of positive feedback from family, friends, and fellow workers who saw the SNS.
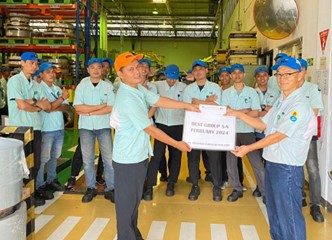